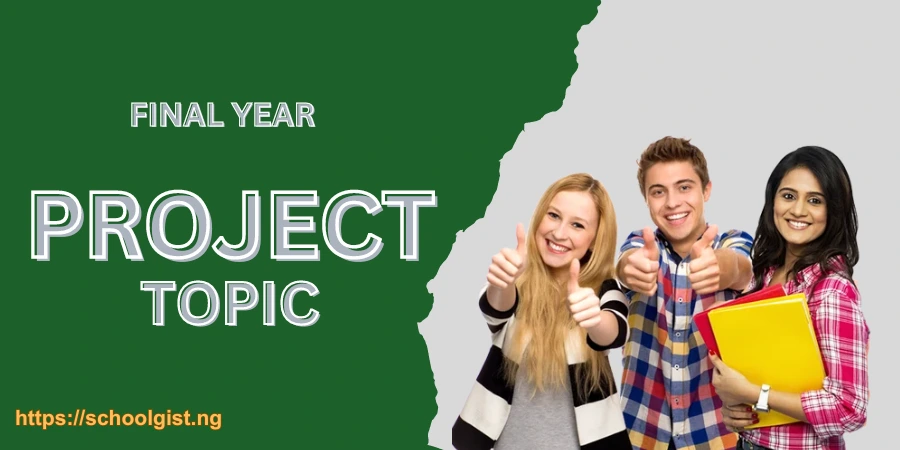
This project work titled THE PRODUCTION OF BIODIESEL (FAME) FROM PALM KERNEL OIL (PKO) USING CONCENTRATED SULPHURIC ACID AS CATALYST has been deemed suitable for Final Year Students/Undergradutes in the Chemistry Department. However, if you believe that this project work will be helpful to you (irrespective of your department or discipline), then go ahead and get it (Scroll down to the end of this article for an instruction on how to get this project work).
Below is a brief overview of this Project Work.
Format: MS WORD
| Chapters: 1-5
| Pages: 60
CHAPTER ONE
INTRODUCTION
1.1 BACKGROUND OF THE STUDY
Energy is a fundamental pillar of modern society as well as being an essential building block for socio-economic development (UNIDO, 2007). The awareness of the imminent depletion of fossil fuels coupled with a global energy crisis has stimulated interest in the research for alternative energy source (Garba et al., 1996). The urgent need for alternative and cheaper energy supplies in Nigeria is increasingly apparent now considering the epileptic supply and distribution of the fossil fuels that have risen beyond the reach of Nigerian rural people (Eze, 2003).
The uses of renewable raw materials significantly contribute to sustainable development usually interpreted as “acting responsibly to meet the needs of the present without compromising the ability of future generations to meet their own needs” (Meier, et al., 2007).
Currently, plant oils are the most important renewable raw materials for the chemical industry. They are triglycerides (tri – esters of glycerol with long chain fatty acid) (see Fig. 1) with varying composition of fatty acids depending on the plant, the crop, the season and the growing conditions.
Biofuels are a wide range of fuels which are derived from biomass and can be used as a large source of energy supply. The term covers solid biomass, liquid fuels and various biogases (Dembras, 2009). Biofuels are gaining increased public and scientific attention, driven by factors such as oil price spikes, the need for increased energy security, concern over greenhouse gas emissions from fossil fuels, and government subsidies.
Biofuels are drawing increasing attention worldwide as substitutes for petroleum – derived transportation fuels to help address energy cost, energy security and global warming concern associated with liquid fossil fuels. Biofuels include ethanol made from sugar cane or diesel-like fuel made from soybean oil, dimethyl ether (DME) or Fischer – Tropsch Liquids (FTL) made from lignocellusosic biomass.
The Energy Commission of Nigeria envisions that in the short term (2005 – 2007), crude oil will continue to play a dominant role in the economic development of the country, while in the medium term (2008 – 2015), a transition in energy from crude oil to less carbon – intensive economy increasingly powered by gas. Also, in the long term (2016 – 2025), the nation’s energy requirement will be completely non fossil. (ECN, 2005).
A relatively recently popularized classification for liquid biofuels includes first generation and second generation fuels. There is no strict technical definitions for these terms but the main distinction between them is the feedstock used.
First generation fuels are generally those made from sugar, grains or seeds, i.e. one that uses only a specific (often edible) portion of the above – ground biomass produced by a plant , and relatively simple processing is required to produce a finished fuel. First generation fuels are already being produced in significant commercial quantities in a number of countries. Members of this group are bioalcohol, biodiesel, green diesel (also known as renewable diesel), bioether, biogas e.t.c.
Second generation fuels are generally those made from non-edible lignocellosic biomass, either non-edible residues of food crop production (e.g. corn stalks or rice husks) or non-edible whole plant biomass (e.g. grasses or trees grown specifically for energy). Second generation biofuels are basically produced from sustainable feedstock. Sustainability of a feedstock is defined among others by availability of the feedstock, impact on greenhouse gas emissions and impact on biodiversity and land use. Many second generation biofuels are under development such as cellusoic ethanol, algae fuel, biohydrogen, biomethanol, Fischer – Tropsch diesel, mixed alcohols, biohydrogen diesel and wood diesel.
Biodiesel (fatty acid methyl esters) is an alternative fuel for diesel engines. It is an alcohol ester product from the transesterification of triglycerides in vegetable oils or animals accomplished by reacting lower alcohols such as methanol or ethanol with triglycerides.
The National Biodiesel Board (USA) technically defined biodiesel as a mono-alkyl ester. Blends of biodiesel and conventional hydrocarbon based diesel are products most commonly distributed for use in the retail diesel fuel market place. Biodiesel contain no petroleum, but it can be blended at any level with petroleum diesel to create a biodiesel blend. Much of the world uses a system known as the “B” factor to state the amount of biodiesel in any fuel mix:
Ø 100% biodiesel is referred to as B100.
Ø 20% biodiesel, 80% petrodiesel is labelled B20.
Ø 5% biodiesel, 95% petrodiesel is labelled B5.
Ø 2% biodiesel, 98% petrodiesel is labelled B2.
Blends of less than 20% biodiesel can be used in diesel equipment with no, or only minor modifications. Biodiesel can also be used in its pure form (B100), but may be blended with petroleum diesel at any concentration in most injection pump diesel engine. New extreme high-pressure (29000 psi) common rail engine have strict factory limits of B5 or B20 depending on manufacturers.
Biodiesel has different solvent properties than petrodiesel, and will degrade natural rubber gaskets and hoses in vehicles (mostly vehicles manufactured before 1992), although these tend to wear out naturally and most likely will have already been replaced with FKM, which is non reactive to biodiesel.
The first diesel engine was produced by Rudolf in Augsburg and Germany. In remembrance of this event, August 10 has been declared “International Biodiesel Day”. Rudolf diesel demonstrated a diesel running on pea nut (at the request of the French government) but for the French otto company at the world fair in Paris, France in 1990. (Knothe, 2001).
Biodiesel has been known to breakdown deposits of residue in the fuel lines where petrodiesel has been used. As a result, fuel filters may become clogged with particulates of a quick transition to pure biodiesel is made. Therefore, it is recommended to change the fuel filters on engine and heaters shortly after switching to a biodiesel blend.
Biodiesel is light to dark yellow liquid immiscible with water, with high boiling point and low vapour pressure. It has been used as a substitute for diesel fuel in the automobile industry and also referred to as a diesel – equivalent processed fuel derived from vegetable oils. (Biodiesel, 2007).
Several research have been performed on the production of biodiesel and some basic feedstock for the fuel includes animal fats, vegetable oils, soy, rapseed, jatropha, mahua, mustard, flax, sunflower, palm oil, hemp, field pennycress, pongamiapinnata and algae. Pure biodiesel is the lowest emission diesel fuel. Although liquefied petroleum gas and hydrogen have cleaner combustion, they are used to fuel much less efficient petrol engines and are not as widely available. Biodiesel is an oxygenated fuel, meaning that it contains a reduced amount of carbon and higher hydrogen and oxygen content than fossil diesel. This improves the combustion and reduces the particulate emission from un-burnt carbon. Biodiesel is also safe to handle and transport because it is as biodegradable as sugar, ten times less toxic than table salt, has a high flash point of about 300oF (148oC) compared to petroleum diesel fuel, which has a flash point of 125oF (52oC).
Current commercial production of biodiesel (FAME) is via homogeneous transesterification but this process has a lot of limitations, thus, making the cost of biodiesel not economical as compared to petroleum-derived diesel. One of the most significant limitations using this process is the formations of soap in the product mixture leading to additional cost required for the separation of soap from the biodiesel. Also, the formation of soap has also led to the loss of triglycerides molecules that can be used to form biodiesel. However, since the catalyst and the reactants/products are in the same phase, the separation of products (biodiesel) from the catalyst becomes complex. On the other hand, heterogeneous transesterification can overcome all these limitations in which solid based catalyst is used in place of homogeneous catalyst, making it a more efficient process for biodiesel production with lower cost and reduced environmental impact.
Xie et al. studied the transesterification of soybean oil to methyl ester using potassium-loaded alumina catalyst. Also, Suppes et al. studied the transesterification reaction of soybean oil with zeolite and metal catalysts for the production of biodiesel, while Jitputti et al. studied the transesterification of crude palm kernel oil and crude coconut oil using several acidic and basic solids.
All these study indicated that different oils would require different catalyst for optimum conversion to biodiesel. {International Conference on Environment 2008 (ICENV 2008)}
How to Download the Full Project Work for FREE
- You can download the Full Project Work for FREE by Clicking Here.
- On the other hand, you can make a payment of ₦6,000 and we will send the Full Project Work directly to your email address or to your Whatsapp. Clicking Here to Make Payment.