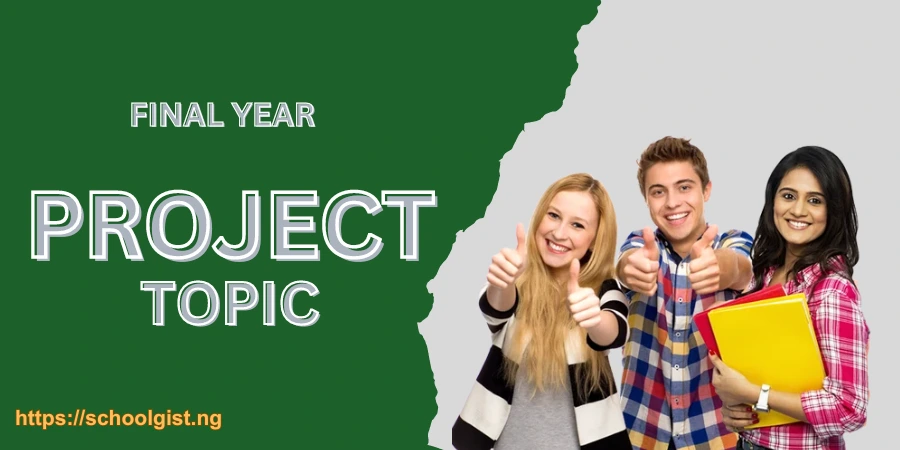
This project work titled THE DESIGN AND CONSTRUCTION OF A MODERN NAIL GASKET MACHINE has been deemed suitable for Final Year Students/Undergradutes in the Mechanical Engineering Department. However, if you believe that this project work will be helpful to you (irrespective of your department or discipline), then go ahead and get it (Scroll down to the end of this article for an instruction on how to get this project work).
Below is a brief overview of this Project Work.
Format: MS WORD
| Chapters: 1-5
| Pages: 59
The design and fabrication of a reciprocating nail gasket is a new innovation in technology. The one in existence is manually operated. In which a punch that is adjacent to a die is mounted to the handle which is attached to the shaft. A helical spring that is incorporated to the shaft of the punch, helps the handle return to its initial position, which makes the machines tedious and stressful to operate. When the handle is pulled down from its initial position, the punch passes through the die that is placed vertically adjacent to the punch thereby blanking out the felt materials. The number of the gasket produced is proportional to the strength of the operator. But in our design, we incorporated a geared motor which does the cutting in a reciprocating form, while the operator just drags the felt material to the die where it is cut. The efficiency of the machine is well above 75%, it can produce 216 felts per minutes . sprockets and chains are used to transfer power instead of belts in other to effect good phases relationship. The material used for the punch is stainless steel rod. The machine is statically and dynamically balanced to curb noise and vibration. One and half (11/2) inch angle iron was used in fabricating the skeletal frame. Appropriate materials were subsequently selected and fabricated to required size. The machine was then to perform efficiently thus satisfying the objective for which it was designed.
CHAPTER ONE
Following the advancement of technology, and the need to eliminate the archaic method of producing nail gasket in this era, which really decreases production. The aim of our improved motorized nail gasket cutting machine, it to increase production drastically and to reduce human fatigue and cost of the product. The materials employed in this design and construction of the machine is mechanically reliable. this work is also helped to act as a catalyst and encouragement towards the promotion of indigenous ingenuity in technological development of our country. And federal government’s involvement in encouraging and funding of degree projects to construct machines that would help the nation. Nigeria is still a developing nation, federal government has mapped out huge money for industrial buildings, housing estates, and foreign investors are coming into the country to invest their various business. This motorized nail gasket producing machines will really boast production and also help increase revenue generated through exportation of the product.
1.2 PURPOSE OF THE STUDY
The machine is existence manually operated in totality of the product produced by the machine is proportional to the strength of the operator. And the manual one is difficult to maintain and durability not guaranteed as in the case of these that used low quality material in construction. This particular work understands the problems, there by incorporating geared motor so that number of gaskets produced will be proportional to the horsepower of the motor i.e production increases.
1.3 SCOPE OF THE STUDY
This design and construction work is considered with only a prototype. A theoretical improvement consideration and design of all components parts of the machine will be guided by the design of standard components. Problems are also covered in other to realized the purpose of the project. This work covers the stages of machine development, design/fabrication of components parts and construction of its parts. Process involved in the design are analyzed. Stresses on deformation forces were given consideration. This report covers detail parts and assembly drawing with recommendation on manufacturing methods. Choice of design was subject to information modification at the energy of many factors beyond strength and rigidity which were important; these include fabrication techniques and material availability.
How to Download the Full Project Work for FREE
- You can download the Full Project Work for FREE by Clicking Here.
- On the other hand, you can make a payment of ₦6,000 and we will send the Full Project Work directly to your email address or to your Whatsapp. Clicking Here to Make Payment.