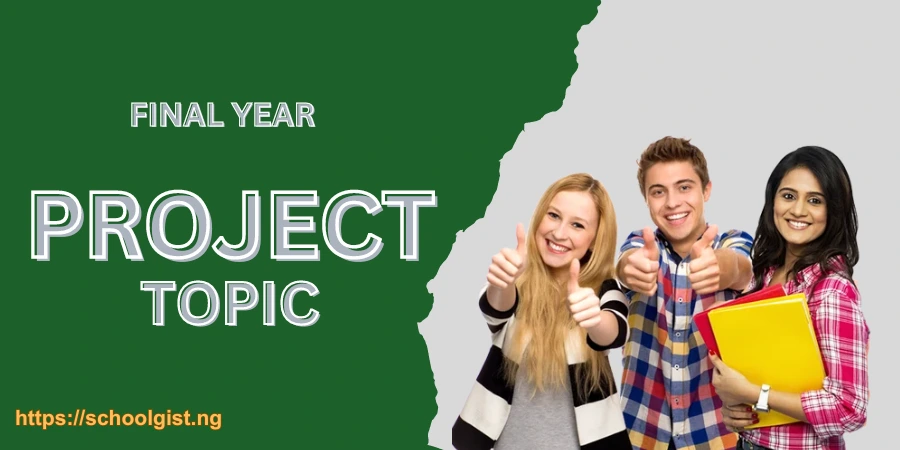
This project work titled STOCK CONTROL: AN INTEGRAL PART OF PROFIT MAXIMISATION (A CASE STUDY OF SEVEN UP BOTTLING COMPANY, LAGOS) has been deemed suitable for Final Year Students/Undergradutes in the Accounting Department. However, if you believe that this project work will be helpful to you (irrespective of your department or discipline), then go ahead and get it (Scroll down to the end of this article for an instruction on how to get this project work).
Below is a brief overview of this Project Work.
Format: MS WORD
| Chapters: 1-5
| Pages: 70
CHAPTER ONE
Every organization has its own purpose of operation and pre-determined goals and objectives to be accomplished in relation to the organization’s mission and vision statement. The level at which goals or objectives can be actualized depends on the efficiency and effectiveness of operation and internal control Mgbonyebi and Umead (2008). . But for the goals of any organization to be achieved, such entity must observe some stipulated or laid down principles for its performance. When these rules are followed simultaneously, then the usefulness of such principle or concept will be achieved. In general term, management has been recognized as the process of planning , organizing, direct and controlling business operation to ensure that states predetermined goals and objectives are accomplished Carter (2012). Agagu (2009) defines management as a process which enables organizations to set and achieve their objectives by planning, organizing, and control their resources including giving the commitment of their employees (motivation).
According to Ama (2001) inventory is described as stock of goods a firm is producing for sales and the components that make up the goods. Hilton (2004) defines inventory as an itemized list of goods (raw materials, finished goods and work in progress) which forms certain proportion of organizations’ investment. In recent years, Inventory Management has attracted a great deal of attention from people both in academia and industries. A lot of resources have been devoted into research in the inventory management practices of organizations. It represents one of the most important assets that most businesses possess, because the turnover of inventory represents one of the primary sources of revenue generation and subsequent earnings for the company. In the manufacturing companies, nearly 60% to 70% of the total funds employed are tied up in current assets, of which inventory is the most significant component Carter (2002). Thus, it should be managed in order to avail the inventories at right time in right quantity. Inventory can be also viewed as an idle resource which has an economic value. So, better management of the inventories would release capital productively. Therefore, from the above definitions inventory is the totality of all the stock, which includes raw materials work-in-progress and finished goods said to be the total amount of goods and materials contained in a store or factory at any given time.
Therefore the aim of this research work is to evaluate how beverage companies as part of manufacturing concerns have been avoiding wastages in inventory by using efficient Inventory managements and control techniques like Economics Order Quantity (EOQ), Just-in-Time (JIT), Quick Response Manufacture (QRM), among others to render efficient services to their customer, maximize profit, avoid production hold-ups in factories and eliminate risk of liquidity crunch, etc. to
Every organization has its own purpose of operation and pre-determined goals and objectives to be accomplished in relation to the organization’s mission and vision statement. The level at which goals or objectives can be actualized depends on the efficiency and effectiveness of operation and internal control Mgbonyebi and Umead (2008). . But for the goals of any organization to be achieved, such entity must observe some stipulated or laid down principles for its performance. When these rules are followed simultaneously, then the usefulness of such principle or concept will be achieved. In general term, management has been recognized as the process of planning , organizing, direct and controlling business operation to ensure that states predetermined goals and objectives are accomplished Carter (2012). Agagu (2009) defines management as a process which enables organizations to set and achieve their objectives by planning, organizing, and control their resources including giving the commitment of their employees (motivation).
According to Ama (2001) inventory is described as stock of goods a firm is producing for sales and the components that make up the goods. Hilton (2004) defines inventory as an itemized list of goods (raw materials, finished goods and work in progress) which forms certain proportion of organizations’ investment. In recent years, Inventory Management has attracted a great deal of attention from people both in academia and industries. A lot of resources have been devoted into research in the inventory management practices of organizations. It represents one of the most important assets that most businesses possess, because the turnover of inventory represents one of the primary sources of revenue generation and subsequent earnings for the company. In the manufacturing companies, nearly 60% to 70% of the total funds employed are tied up in current assets, of which inventory is the most significant component Carter (2002). Thus, it should be managed in order to avail the inventories at right time in right quantity. Inventory can be also viewed as an idle resource which has an economic value. So, better management of the inventories would release capital productively. Therefore, from the above definitions inventory is the totality of all the stock, which includes raw materials work-in-progress and finished goods said to be the total amount of goods and materials contained in a store or factory at any given time.
Therefore the aim of this research work is to evaluate how beverage companies as part of manufacturing concerns have been avoiding wastages in inventory by using efficient Inventory managements and control techniques like Economics Order Quantity (EOQ), Just-in-Time (JIT), Quick Response Manufacture (QRM), among others to render efficient services to their customer, maximize profit, avoid production hold-ups in factories and eliminate risk of liquidity crunch, etc. to
How to Download the Full Project Work for FREE
- You can download the Full Project Work for FREE by Clicking Here.
- On the other hand, you can make a payment of ₦5,000 and we will send the Full Project Work directly to your email address or to your Whatsapp. Clicking Here to Make Payment.