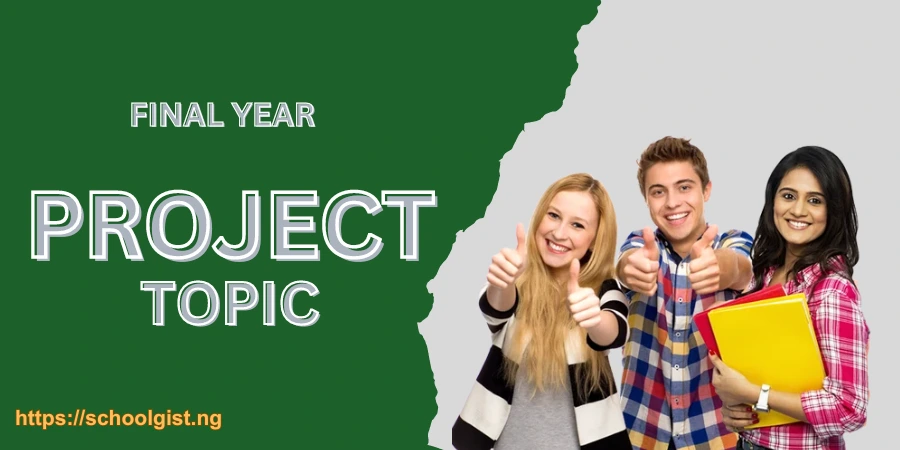
This project work titled SAFETY MANAGEMENT PROGRAMME IN MANUFACTURING FIRM has been deemed suitable for Final Year Students/Undergradutes in the Business Administration Department. However, if you believe that this project work will be helpful to you (irrespective of your department or discipline), then go ahead and get it (Scroll down to the end of this article for an instruction on how to get this project work).
Below is a brief overview of this Project Work.
Format: MS WORD
| Chapters: 1-5
| Pages: 52
SAFETY MANAGEMENT PROGRAMME IN MANUFACTURING FIRM
CHAPTER ONE
INTRODUCTION
1.1 BACKGROUND TO THE STUDY
There is no double that industry is one of the most important sectors of the economy. The fact that a major share of the nations yearly budget goes to the industrial sector remains a testimony. InNigeriaindustrialization, virtually unknown twenty years ago is providing the much needed new dimension into which the national economy can expand and diversity. With dynamism in industrial activities, new and modern sophisticated technology is involved, when these equipment are not used by trained workers, accidents could result because of wrong handling causing damage to equipment and the advice that why brain (1990) gain the advice that safety awareness should be created in the minds of management of all manufacturing organization no matter their size or level of growth. It goes without saying that accidents occur in an industry and if not minimized or checked would ultimately affected productive capacity of the workers as well as the management of the industry and economy in general.
Having known that accidents prevent organization from accomplishing objectives and goals, the question now should be, what measures are the 50- called management of industry doing to ameliorate, if not totally eradicate the rate of injury and accidents occurrence in the government owned industry. The managers are expected to be at the upper echelon, introducing measures and mounting pressure to ensure safety and protection against. Their hazards and accident in the work environment. Unfortunately some management look at safety programme as added cost to the organization hence, they have tended to relent to forestalling the possible hazard in the firm.
In addition to this, Shublin in Udeze (2010) indicated that management should realize that reduction of accident covers their high direct and indirect accident costs of more than pay for the expense of a continuing safety programme. There has been a lot of hues and cries calling for the attention of the management towards work safety, there has equally been a factory act of 1958 which stipulates certain safety standards in manufacturing companies; there has also been the government insistence that safety should be given priority attention as a part of the social responsibility of the organization it is in the light of all these that this study has embarked on finding out the impact of safety management on workers performance in government owned industries. But the problem has often been that management that employees does not feel responsible for ensuring that such hazards are removed. The safety management programme that should trail industrialization is lacking.
1.2 PROBLEMS OF THE STUDY
Accident and hazards are the inevitable phenomenon of any human organization but the concern of every rational and curious researcher is on the measures that should be applied to minimize the occurrence of accident in government owned industry. Furthermore, it is difficult to described a situation in which in spite of various academics writes ups government concerned about workers safety. This is why Anibata (1991:38) in his analysis opi9ned that as industrial workers depends on his employer, as being able to providing him with his safety requirements needed for his work and to receive some compensation when his health is affected, these requirement when absent creates laxity in workers.
Workers in the government owned industry are often injured, maimed and incapacitated as a result of industrial resident and to add that some management are not even aware of their role and responsibility as regards to industrial accident. Though some argue that however careful we are, accident can still happen but, what of a situation where workers are not given adequate training or where management are not concerned about safety. For the employees to be committed and work toward achieving organizational goal and objective their own individual need and aspiration must also be met. Thus, it is the responsibility of the management to ensure that all employees are properly equipped and trained so that employee would work safety and productively.
Good safety behaviour should be a condition of employment and should be treated in the same way as any other performance criterion. Poor safety performance in any section of the business demands correction which good performance needs recognition. There fore, management to achieve its set goals must foster and nurture a committed work force, which can be achieved by setting their aspiration fulfilled. Attention channeled towards improving the environment upon where workers work and their safety considerations, help in goal attainment for example, a Nigerian worker who feels that his life is as stake when operating a machine without adequate protective equipment might not put his best no matter the monetary rewards because life has no duplicate.
1.3 RESEARCH QUESTIONS
The following research question were used to draft the questionnaire to the study .
i. How does your company ensure effective implementation of her safety management programme?
ii. What are the positive effects on workers performance that result from the implementation of your company’s safety management prgramme?
iii. How secure is your place of work against factory accidents?
iv. What are the negative effects that your company’s safety management programmes have on workers performance?
1.4 SCOPE OF THE STUDY
This study on the impact of safety management programme in Nigeriaindustries would benefit the workers, companies andNigeriain general if implemented for instance. Would emphasize the role of the working supervisors and the importance of his responsibilities for the safe operation of plants control of people in a hazardous working environment. Would emphasize the type of training needed and given to the worker about safety at work place and developing safety consciousness. Would motivate staff to work safety for the benefit of themselves, other and to the nation. It will bring about a major improvement in safety performance in a way that will be sustained.
1.5 DEFINITION OF IMPORTANT TERMS
The following terms have been used in a number of places in the study for the purpose of this research they have been used in the following sense .
SAFETY- Freedom from accident in the work place.
ACCIDENT- Any unpredicted unplanned event, which could result in personal in jury, damage to plant, in creased cast, loss of production and population of the environment.
HAZARD- A hazard is any condition that might operate against the safety workers.
IMPACT- The impression the programme made on the workers.
PERFORMANCE- What is accomplished contrasted with capacity.
PPE- Personal protection equipment
REFERENCE
AnibataI.(2011) “ Risk Management inNigeriaStation Information “ Booklet Vo. 12.
Brain G. (2010) “Safety at Work” in information Booklet on H.S.E (WarriSDC Corporate Re. Prographic Center).
Udeze J.O (2010) “Human Resources” Management inNigeria,EnuguJoe Best Books.
CHAPTER ONE
INTRODUCTION
1.1 BACKGROUND TO THE STUDY
There is no double that industry is one of the most important sectors of the economy. The fact that a major share of the nations yearly budget goes to the industrial sector remains a testimony. InNigeriaindustrialization, virtually unknown twenty years ago is providing the much needed new dimension into which the national economy can expand and diversity. With dynamism in industrial activities, new and modern sophisticated technology is involved, when these equipment are not used by trained workers, accidents could result because of wrong handling causing damage to equipment and the advice that why brain (1990) gain the advice that safety awareness should be created in the minds of management of all manufacturing organization no matter their size or level of growth. It goes without saying that accidents occur in an industry and if not minimized or checked would ultimately affected productive capacity of the workers as well as the management of the industry and economy in general.
Having known that accidents prevent organization from accomplishing objectives and goals, the question now should be, what measures are the 50- called management of industry doing to ameliorate, if not totally eradicate the rate of injury and accidents occurrence in the government owned industry. The managers are expected to be at the upper echelon, introducing measures and mounting pressure to ensure safety and protection against. Their hazards and accident in the work environment. Unfortunately some management look at safety programme as added cost to the organization hence, they have tended to relent to forestalling the possible hazard in the firm.
In addition to this, Shublin in Udeze (2010) indicated that management should realize that reduction of accident covers their high direct and indirect accident costs of more than pay for the expense of a continuing safety programme. There has been a lot of hues and cries calling for the attention of the management towards work safety, there has equally been a factory act of 1958 which stipulates certain safety standards in manufacturing companies; there has also been the government insistence that safety should be given priority attention as a part of the social responsibility of the organization it is in the light of all these that this study has embarked on finding out the impact of safety management on workers performance in government owned industries. But the problem has often been that management that employees does not feel responsible for ensuring that such hazards are removed. The safety management programme that should trail industrialization is lacking.
1.2 PROBLEMS OF THE STUDY
Accident and hazards are the inevitable phenomenon of any human organization but the concern of every rational and curious researcher is on the measures that should be applied to minimize the occurrence of accident in government owned industry. Furthermore, it is difficult to described a situation in which in spite of various academics writes ups government concerned about workers safety. This is why Anibata (1991:38) in his analysis opi9ned that as industrial workers depends on his employer, as being able to providing him with his safety requirements needed for his work and to receive some compensation when his health is affected, these requirement when absent creates laxity in workers.
Workers in the government owned industry are often injured, maimed and incapacitated as a result of industrial resident and to add that some management are not even aware of their role and responsibility as regards to industrial accident. Though some argue that however careful we are, accident can still happen but, what of a situation where workers are not given adequate training or where management are not concerned about safety. For the employees to be committed and work toward achieving organizational goal and objective their own individual need and aspiration must also be met. Thus, it is the responsibility of the management to ensure that all employees are properly equipped and trained so that employee would work safety and productively.
Good safety behaviour should be a condition of employment and should be treated in the same way as any other performance criterion. Poor safety performance in any section of the business demands correction which good performance needs recognition. There fore, management to achieve its set goals must foster and nurture a committed work force, which can be achieved by setting their aspiration fulfilled. Attention channeled towards improving the environment upon where workers work and their safety considerations, help in goal attainment for example, a Nigerian worker who feels that his life is as stake when operating a machine without adequate protective equipment might not put his best no matter the monetary rewards because life has no duplicate.
1.3 RESEARCH QUESTIONS
The following research question were used to draft the questionnaire to the study .
i. How does your company ensure effective implementation of her safety management programme?
ii. What are the positive effects on workers performance that result from the implementation of your company’s safety management prgramme?
iii. How secure is your place of work against factory accidents?
iv. What are the negative effects that your company’s safety management programmes have on workers performance?
1.4 SCOPE OF THE STUDY
This study on the impact of safety management programme in Nigeriaindustries would benefit the workers, companies andNigeriain general if implemented for instance. Would emphasize the role of the working supervisors and the importance of his responsibilities for the safe operation of plants control of people in a hazardous working environment. Would emphasize the type of training needed and given to the worker about safety at work place and developing safety consciousness. Would motivate staff to work safety for the benefit of themselves, other and to the nation. It will bring about a major improvement in safety performance in a way that will be sustained.
1.5 DEFINITION OF IMPORTANT TERMS
The following terms have been used in a number of places in the study for the purpose of this research they have been used in the following sense .
SAFETY- Freedom from accident in the work place.
ACCIDENT- Any unpredicted unplanned event, which could result in personal in jury, damage to plant, in creased cast, loss of production and population of the environment.
HAZARD- A hazard is any condition that might operate against the safety workers.
IMPACT- The impression the programme made on the workers.
PERFORMANCE- What is accomplished contrasted with capacity.
PPE- Personal protection equipment
REFERENCE
AnibataI.(2011) “ Risk Management inNigeriaStation Information “ Booklet Vo. 12.
Brain G. (2010) “Safety at Work” in information Booklet on H.S.E (WarriSDC Corporate Re. Prographic Center).
Udeze J.O (2010) “Human Resources” Management inNigeria,EnuguJoe Best Books.
How to Download the Full Project Work for FREE
- You can download the Full Project Work for FREE by Clicking Here.
- On the other hand, you can make a payment of ₦5,000 and we will send the Full Project Work directly to your email address or to your Whatsapp. Clicking Here to Make Payment.