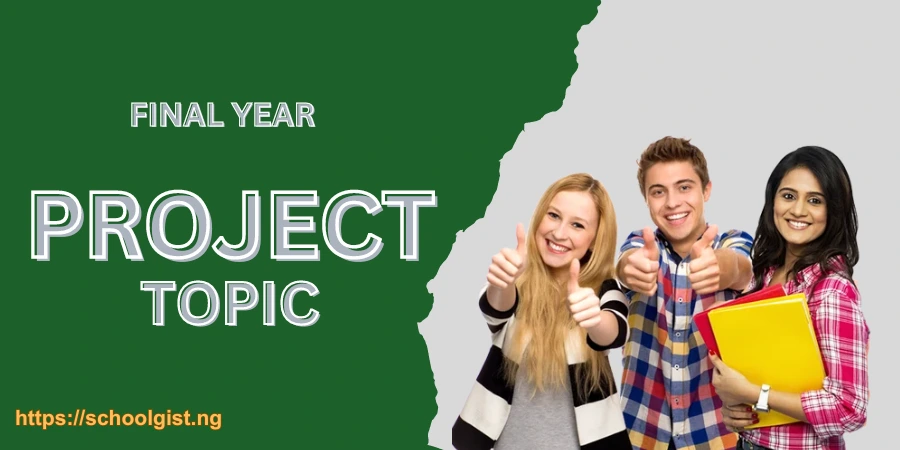
This project work titled MANAGEMENT OF EMPLOYEE WELFARE WITH EMPHASIS ON INDUSTRIAL ACCIDENTS AND SAFETY has been deemed suitable for Final Year Students/Undergradutes in the Human Resource Management Department. However, if you believe that this project work will be helpful to you (irrespective of your department or discipline), then go ahead and get it (Scroll down to the end of this article for an instruction on how to get this project work).
Below is a brief overview of this Project Work.
Format: MS WORD
| Chapters: 1-5
| Pages: 61
MANAGEMENT OF EMPLOYEE WELFARE WITH EMPHASIS ON INDUSTRIAL ACCIDENTS AND SAFETY
CHAPTER ONE
INTRODUCTION
1.1 BACKGROUND OF THE STUDY
The industrial revolution of the mid 18th century significantly changed the world of work by introduction machinery. Work moved away from being predominantly agricultural (based on peasantry and tendal land tenures) to factors labor truly became a commodity as workers received only wages for their efforts.
The factory system of production needs four categories of inputs: money to finance operation, machines to produce goods and services, men to operate the machines and managements to put every other thing together. Machines are complex pieces of equipment which a worker has to master to operate. The worker operating machines is usually not the inventor or designer, (like under the domestic or craft system of production). The skill with which a worker operates a machine affected the efficiency of production and the safety and health of the worker.
The situation arises because factory work involved machines that worked at considerable high speeds and which can infeflict injures if great acre is not taken. Also the factory system requires workers to work at a position or within a limited area, doing what are commonly monotonous tasks.
Attention can easily wave when work is monotonous and a person who works at a point (like assembly line worker) may be subjected to physical and physical ecological strain and stress. When this is combined with the speed of operation of machines, the producer of management health and safety becomes easy to appreciate.
There are many definition of the work accident psychologists Arbous A.G and Kerrick J. consider that “in a chain of events each of which is planned or controlled, there occurs an unplanned event which is termed accident”. Schulzinger (1978) also regards accidents as sudden, unplanned and uncontrolled event.
Perhaps a simple definition of an industrial accident is “a mishap resulting in damage to property and or injury or death to person”. It will so far be considered for this research so as to enable us have a quick examination of some of the factors causing occupational or industrial and diseases.
1.2 STATEMENT OF THE PROBLEMS
Accidents are mishaps and may result in damage to property and or injury or death to persons whilst accidents are unplanned for, their adverse effects can be managed by industrial safety programs. Principal items in an industrial safety program include, Engineering a stage machine and operating manual, educating all employees to act safety deeply accurate record of operational accidents ill-health, a injures and deaths, accident analysis safety contests and enforcing the release (flip, 1980). Employee morale impacts on productivity the better the morale, the higher the productivity. Industrial accidents reduce productivity (and actual reduce production). It can be inferred that boosting morale can reduce accidents. Facility design and layout contribute to employee morale. Besides morale equipments failure reduces productivity and increase industrial accidents.
We can therefore say that there are tow categories of causes of industrial accidents technical and human. Technical causes are connected with deficiencies in factories, machine tool, materials, and the general working environment. On the other hand, human causes are connected with deficiencies in the individual. Such as improper attitudes carelessness, recklessness, inability to perform the job, day-dreaming alcoholism and the use of the drugs on the job. It is estimated that out of five accident in industry are caused by human deficiencies (flip 1980). When accidents occur damage, injury of death may result, each of these involve some form of cost both direct and indirect. There are some problem associated in NB PLC 9th mile corner Enugu and they are as follows.
1. ILLITERACY: The majority of the workers are half educated ones and many don’t know when information was sending and what it talks about.
2. Some managers are disillusioned because major decisions effecting their departments are taken without them was being contracted.
3. OVER LOADING: The overloading of the machines causes accidents.
4. Bad construction and design of machine.
5. NOISE: There are relationship between noise and accidents rate but evidence in support of this is not over whelming.
CHAPTER ONE
INTRODUCTION
1.1 BACKGROUND OF THE STUDY
The industrial revolution of the mid 18th century significantly changed the world of work by introduction machinery. Work moved away from being predominantly agricultural (based on peasantry and tendal land tenures) to factors labor truly became a commodity as workers received only wages for their efforts.
The factory system of production needs four categories of inputs: money to finance operation, machines to produce goods and services, men to operate the machines and managements to put every other thing together. Machines are complex pieces of equipment which a worker has to master to operate. The worker operating machines is usually not the inventor or designer, (like under the domestic or craft system of production). The skill with which a worker operates a machine affected the efficiency of production and the safety and health of the worker.
The situation arises because factory work involved machines that worked at considerable high speeds and which can infeflict injures if great acre is not taken. Also the factory system requires workers to work at a position or within a limited area, doing what are commonly monotonous tasks.
Attention can easily wave when work is monotonous and a person who works at a point (like assembly line worker) may be subjected to physical and physical ecological strain and stress. When this is combined with the speed of operation of machines, the producer of management health and safety becomes easy to appreciate.
There are many definition of the work accident psychologists Arbous A.G and Kerrick J. consider that “in a chain of events each of which is planned or controlled, there occurs an unplanned event which is termed accident”. Schulzinger (1978) also regards accidents as sudden, unplanned and uncontrolled event.
Perhaps a simple definition of an industrial accident is “a mishap resulting in damage to property and or injury or death to person”. It will so far be considered for this research so as to enable us have a quick examination of some of the factors causing occupational or industrial and diseases.
1.2 STATEMENT OF THE PROBLEMS
Accidents are mishaps and may result in damage to property and or injury or death to persons whilst accidents are unplanned for, their adverse effects can be managed by industrial safety programs. Principal items in an industrial safety program include, Engineering a stage machine and operating manual, educating all employees to act safety deeply accurate record of operational accidents ill-health, a injures and deaths, accident analysis safety contests and enforcing the release (flip, 1980). Employee morale impacts on productivity the better the morale, the higher the productivity. Industrial accidents reduce productivity (and actual reduce production). It can be inferred that boosting morale can reduce accidents. Facility design and layout contribute to employee morale. Besides morale equipments failure reduces productivity and increase industrial accidents.
We can therefore say that there are tow categories of causes of industrial accidents technical and human. Technical causes are connected with deficiencies in factories, machine tool, materials, and the general working environment. On the other hand, human causes are connected with deficiencies in the individual. Such as improper attitudes carelessness, recklessness, inability to perform the job, day-dreaming alcoholism and the use of the drugs on the job. It is estimated that out of five accident in industry are caused by human deficiencies (flip 1980). When accidents occur damage, injury of death may result, each of these involve some form of cost both direct and indirect. There are some problem associated in NB PLC 9th mile corner Enugu and they are as follows.
1. ILLITERACY: The majority of the workers are half educated ones and many don’t know when information was sending and what it talks about.
2. Some managers are disillusioned because major decisions effecting their departments are taken without them was being contracted.
3. OVER LOADING: The overloading of the machines causes accidents.
4. Bad construction and design of machine.
5. NOISE: There are relationship between noise and accidents rate but evidence in support of this is not over whelming.
How to Download the Full Project Work for FREE
- You can download the Full Project Work for FREE by Clicking Here.
- On the other hand, you can make a payment of ₦5,000 and we will send the Full Project Work directly to your email address or to your Whatsapp. Clicking Here to Make Payment.