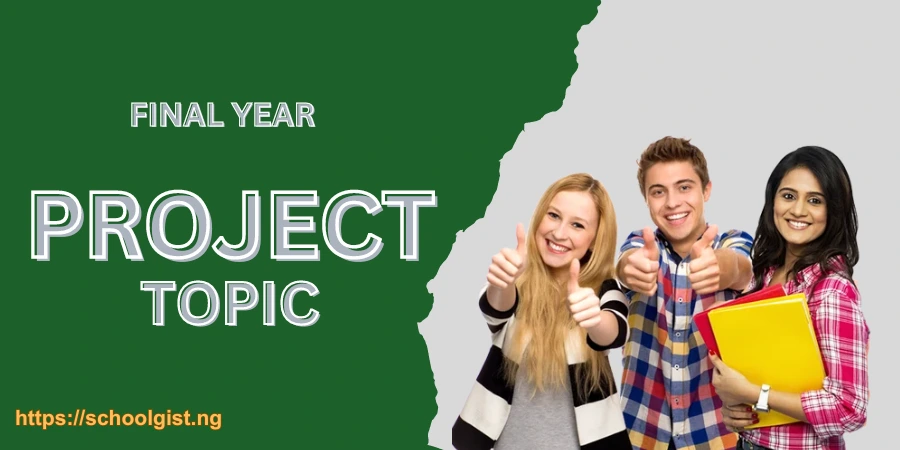
This project work titled INVENTORY MANAGEMENT AND ORGANIZATIONAL PRODUCTIVITY (A CASE STUDY OF COCA-COLA COMPANY PORT HARCOURT BRANCH) has been deemed suitable for Final Year Students/Undergradutes in the Accounting Department. However, if you believe that this project work will be helpful to you (irrespective of your department or discipline), then go ahead and get it (Scroll down to the end of this article for an instruction on how to get this project work).
Below is a brief overview of this Project Work.
Format: MS WORD
| Chapters: 1-5
| Pages: 65
INVENTORY MANAGEMENT AND ORGANIZATIONAL PRODUCTIVITY (A CASE STUDY OF COCA-COLA COMPANY PORT HARCOURT BRANCH)
CHAPTER ONE
INTRODUCTION
1.1 BACKGROUND OF STUDY
Companies face a dilemma in today’s competitive marketplace, where on one hand, customer demand customized products and services and require that their orders are filled quickly, but on the other hand they do not want to pay a premium for this customization and availability (Vohra 2008). Therefore, organizations are exploring ways towards postponement strategy in response to constantly changing demands. Vohra 2008 argued that today, the cost of holding, extensive product proliferation and the risk of obsolescence, especially in rapidly changing markets, make the expense of holding large inventories of finished goods excessive and that high demand items naturally have safety stock assigned to them, but in many organization there are so many very-low-demand items that keeping any stock of these items is unreasonably expensive, so they argue that companies must now provide good services while maintaining minimal inventories. Therefore, inventory management approaches are essential aspects of any organization.
In traditional settings, inventories of raw materials, work-in-progress components and finished goods were kept as a buffer against the possibility of running out of needed items. However, large buffer inventories consume valuable resources and generate hidden costs. Consequently, many companies have changed their approach to production and inventory management. Since at least the early 1980s, inventory management leading to inventory reduction has become the primary target, as is often the case in just-in-time(jit) systems, where raw materials and parts are purchased or produced just in time to be used at each stage of the production process. This approach to inventory management brings considerable cost savings from reduced inventory levels. As a result, inventories have been decreasing in many firms (Sawaya Jr.and Grauquw,2006),although evidence of improved firm organizational productivity is mixed(Tement et al(2010).
The role inventory management is to ensure faster inventory turnover. It increases inventory turnover by ten(10) and reduce costs by 10% to 40%. The so called inventory turnover is not yet right to sell product on the shelves based on the principle of fifo cycle (Kenneth lyson sans Moore et al,2003).
Inventory is classified basing on the business undertaking from organization to organization. Common criteria used and are nature of inventory for example manufacturing, sale or retail, purpose for which inventory is being held in stock or function and the related usage in the supply chain. Typical classifications are raw materials (items in unprocessed state awaiting conversion e.g. timber, steel and coffee seeds), components and sub-assembles. These are for incorporation into the end product e.g. side mirrors,glasses for car assembling company and monitor or keyboards for a computer assembling company), consumable ( all supplies in an undertaking which are classified as indirect and which do not form part of saleable product.(divided into production, maintenance, office and welfare). Proper classification of inventory and its control improve the financial position of a business (David Jessop and Johnson,2008).
Inventory management is primarily about specifying the size and placement of stocked goods. Inventory management is required at different locations within a facility or within multiple locations of a supply networks to protect the regular and planned course of production against the random disturbance of running out of material or goods for improved organizational productivity (Essary 2010). The scope of inventory management also concerns the fine lines between replenishment lead time, carrying costs of inventory, asset management, inventory forecasting, inventory valuation, inventory visibility, future inventory price forecasting, physical inventory, available physical space for inventory, quality management, replenishment, returns and defective goods and demand forecasting(Vohra 2008:427).
Inventory management involves the planning, ordering and scheduling of the materials used in the manufacturing process. It exercises management over three types of inventories that is raw materials, work in progress and finished goods. Purchasing is primary concerned with management over the raw materials inventory, which includes; raw materials or semi-processed materials, fabricated parts and items (maintenance, repair and operations) Jonah 2011.
1.2 STATEMENT OF THE PROBLEM
Inventory management at Coca cola Port Harcourt plant is mostly seen in arrangement of crates at the plant, bottles packing, buying of raw materials, supply of customers, issuing of raw materials for use in the plant departments. This is because the company uses different systems in inventory management including integrated system(system application and products) responsible for management information system which helps to make serious decision son stock, material requirement points, and over stock brands for the fast moving products.
However these techniques for inventory management at coca-cola, organizational productivity of the company had reduced from 80% to60% in the years 2014 and 2015 respectively. Basing on the above information, coca cola Port Harcourt plant has registered decline in sales organizational productivity over time (Arinaitwe, 2009). The study was set to investigate the relationship between inventory management on organizational productivity of coca cola plant-port Harcourt.
1.3 OBJECTIVE OF THE STUDY
The objective of the study was to find out the inventory management and organizational productivity of private organizations in Nigeria while considering coca cola plant-port Harcourt:
1. To examine the technique of inventory management in coca-cola company port Harcourt.
2. To identify the relationship between inventory management and organizational productivity.
3. To examine the problems associated with inventory management in coca-cola company port Harcourt.
4. To examine how effective inventory management improved organizational productivity in coca-cola company port Harcourt.
1.4 TEST OF HYPOTHESIS
Ho: There is no significant relationship between inventory management and organizational productivity.
H1: There is a significant relationship between inventory management and organizational productivity.
1.4 RESEARCH QUESTIONS
1. What are the techniques of inventory management used in coca- cola port Harcourt branch?
2. What is the relationship between inventory management and organizational productivity in coca-cola company port Harcourt branch?
3. What are the problems associated with inventory management in coca-cola company port Harcourt branch on inventory management?
4. To what extent inventory management improve organizational productivity?
1.5 SIGNIFICANCE OF THE STUDY
The study findings may be significant in the following ways; it is hoped that study findings may be used as basis for further research and investigations in form of literature.
The findings may provide information to managers in different organizations especially on knowing how to compare actual organizational productivity and inventory management.
The findings may also be beneficial to other upcoming researchers to investigate further about the impact of inventory management on organizational productivity of other organizations other than coca- cola plant-port Harcourt.
The study may further encourage government to set up educational institutions to provide training on how to manage inventory in organizations.
1.6 SCOPE OF THE STUDY
The scope of this study borders on inventory management and organizational productivity, case study of coca cola its effects on the performance of business organization and manufacturing industries in particular.
Also, many areas such as inventory management systems, contribution of efficient inventory management to productivity, material issues, costs minimization and economy of operation, the impact of efficient inventory management especially as it concerns the area of study.
1.7 LIMITATION OF THE STUDY
Limitations and factors and this research study are as follows: the time required for the research and the submission of this work is very short and the researcher was unable to go through all organizational productivity companies. Limited Exit:- due to the fact that exact is very difficult to get and school, proper research was not carried out and this affected the integrity of the results achieved.
The management of coca cola breweries prohibited its employees from giving out and information about the company to outsiders without adequate permission from the management and even when this permission was obtained at the long run, many vital and formation were not revealed because they were regarded as the privacy of the company.
1.8 DEFINITION OF TERMS
Inventory: Is the amount of goods, materials or part carried out in stock or store house for example, work in progress (w.i.p), raw materials, financial goods resale more items.
Productivity: The effectiveness of productive effort, especially in industry, as measured in terms of the rate of output per unit of input.
Organization: An organized body of people with a particular purpose, especially a business, society, association, etc.
Inventory management: Inventory management is a science primarily about specifying the shape and placement of stocked goods. It is required at different locations within a facility or within many locations of a supply networks to precede the regular and planned course of production and stock of raw materials.
Get the complete project »
CHAPTER ONE
INTRODUCTION
1.1 BACKGROUND OF STUDY
Companies face a dilemma in today’s competitive marketplace, where on one hand, customer demand customized products and services and require that their orders are filled quickly, but on the other hand they do not want to pay a premium for this customization and availability (Vohra 2008). Therefore, organizations are exploring ways towards postponement strategy in response to constantly changing demands. Vohra 2008 argued that today, the cost of holding, extensive product proliferation and the risk of obsolescence, especially in rapidly changing markets, make the expense of holding large inventories of finished goods excessive and that high demand items naturally have safety stock assigned to them, but in many organization there are so many very-low-demand items that keeping any stock of these items is unreasonably expensive, so they argue that companies must now provide good services while maintaining minimal inventories. Therefore, inventory management approaches are essential aspects of any organization.
In traditional settings, inventories of raw materials, work-in-progress components and finished goods were kept as a buffer against the possibility of running out of needed items. However, large buffer inventories consume valuable resources and generate hidden costs. Consequently, many companies have changed their approach to production and inventory management. Since at least the early 1980s, inventory management leading to inventory reduction has become the primary target, as is often the case in just-in-time(jit) systems, where raw materials and parts are purchased or produced just in time to be used at each stage of the production process. This approach to inventory management brings considerable cost savings from reduced inventory levels. As a result, inventories have been decreasing in many firms (Sawaya Jr.and Grauquw,2006),although evidence of improved firm organizational productivity is mixed(Tement et al(2010).
The role inventory management is to ensure faster inventory turnover. It increases inventory turnover by ten(10) and reduce costs by 10% to 40%. The so called inventory turnover is not yet right to sell product on the shelves based on the principle of fifo cycle (Kenneth lyson sans Moore et al,2003).
Inventory is classified basing on the business undertaking from organization to organization. Common criteria used and are nature of inventory for example manufacturing, sale or retail, purpose for which inventory is being held in stock or function and the related usage in the supply chain. Typical classifications are raw materials (items in unprocessed state awaiting conversion e.g. timber, steel and coffee seeds), components and sub-assembles. These are for incorporation into the end product e.g. side mirrors,glasses for car assembling company and monitor or keyboards for a computer assembling company), consumable ( all supplies in an undertaking which are classified as indirect and which do not form part of saleable product.(divided into production, maintenance, office and welfare). Proper classification of inventory and its control improve the financial position of a business (David Jessop and Johnson,2008).
Inventory management is primarily about specifying the size and placement of stocked goods. Inventory management is required at different locations within a facility or within multiple locations of a supply networks to protect the regular and planned course of production against the random disturbance of running out of material or goods for improved organizational productivity (Essary 2010). The scope of inventory management also concerns the fine lines between replenishment lead time, carrying costs of inventory, asset management, inventory forecasting, inventory valuation, inventory visibility, future inventory price forecasting, physical inventory, available physical space for inventory, quality management, replenishment, returns and defective goods and demand forecasting(Vohra 2008:427).
Inventory management involves the planning, ordering and scheduling of the materials used in the manufacturing process. It exercises management over three types of inventories that is raw materials, work in progress and finished goods. Purchasing is primary concerned with management over the raw materials inventory, which includes; raw materials or semi-processed materials, fabricated parts and items (maintenance, repair and operations) Jonah 2011.
1.2 STATEMENT OF THE PROBLEM
Inventory management at Coca cola Port Harcourt plant is mostly seen in arrangement of crates at the plant, bottles packing, buying of raw materials, supply of customers, issuing of raw materials for use in the plant departments. This is because the company uses different systems in inventory management including integrated system(system application and products) responsible for management information system which helps to make serious decision son stock, material requirement points, and over stock brands for the fast moving products.
However these techniques for inventory management at coca-cola, organizational productivity of the company had reduced from 80% to60% in the years 2014 and 2015 respectively. Basing on the above information, coca cola Port Harcourt plant has registered decline in sales organizational productivity over time (Arinaitwe, 2009). The study was set to investigate the relationship between inventory management on organizational productivity of coca cola plant-port Harcourt.
1.3 OBJECTIVE OF THE STUDY
The objective of the study was to find out the inventory management and organizational productivity of private organizations in Nigeria while considering coca cola plant-port Harcourt:
1. To examine the technique of inventory management in coca-cola company port Harcourt.
2. To identify the relationship between inventory management and organizational productivity.
3. To examine the problems associated with inventory management in coca-cola company port Harcourt.
4. To examine how effective inventory management improved organizational productivity in coca-cola company port Harcourt.
1.4 TEST OF HYPOTHESIS
Ho: There is no significant relationship between inventory management and organizational productivity.
H1: There is a significant relationship between inventory management and organizational productivity.
1.4 RESEARCH QUESTIONS
1. What are the techniques of inventory management used in coca- cola port Harcourt branch?
2. What is the relationship between inventory management and organizational productivity in coca-cola company port Harcourt branch?
3. What are the problems associated with inventory management in coca-cola company port Harcourt branch on inventory management?
4. To what extent inventory management improve organizational productivity?
1.5 SIGNIFICANCE OF THE STUDY
The study findings may be significant in the following ways; it is hoped that study findings may be used as basis for further research and investigations in form of literature.
The findings may provide information to managers in different organizations especially on knowing how to compare actual organizational productivity and inventory management.
The findings may also be beneficial to other upcoming researchers to investigate further about the impact of inventory management on organizational productivity of other organizations other than coca- cola plant-port Harcourt.
The study may further encourage government to set up educational institutions to provide training on how to manage inventory in organizations.
1.6 SCOPE OF THE STUDY
The scope of this study borders on inventory management and organizational productivity, case study of coca cola its effects on the performance of business organization and manufacturing industries in particular.
Also, many areas such as inventory management systems, contribution of efficient inventory management to productivity, material issues, costs minimization and economy of operation, the impact of efficient inventory management especially as it concerns the area of study.
1.7 LIMITATION OF THE STUDY
Limitations and factors and this research study are as follows: the time required for the research and the submission of this work is very short and the researcher was unable to go through all organizational productivity companies. Limited Exit:- due to the fact that exact is very difficult to get and school, proper research was not carried out and this affected the integrity of the results achieved.
The management of coca cola breweries prohibited its employees from giving out and information about the company to outsiders without adequate permission from the management and even when this permission was obtained at the long run, many vital and formation were not revealed because they were regarded as the privacy of the company.
1.8 DEFINITION OF TERMS
Inventory: Is the amount of goods, materials or part carried out in stock or store house for example, work in progress (w.i.p), raw materials, financial goods resale more items.
Productivity: The effectiveness of productive effort, especially in industry, as measured in terms of the rate of output per unit of input.
Organization: An organized body of people with a particular purpose, especially a business, society, association, etc.
Inventory management: Inventory management is a science primarily about specifying the shape and placement of stocked goods. It is required at different locations within a facility or within many locations of a supply networks to precede the regular and planned course of production and stock of raw materials.
Get the complete project »
How to Download the Full Project Work for FREE
- You can download the Full Project Work for FREE by Clicking Here.
- On the other hand, you can make a payment of ₦5,000 and we will send the Full Project Work directly to your email address or to your Whatsapp. Clicking Here to Make Payment.