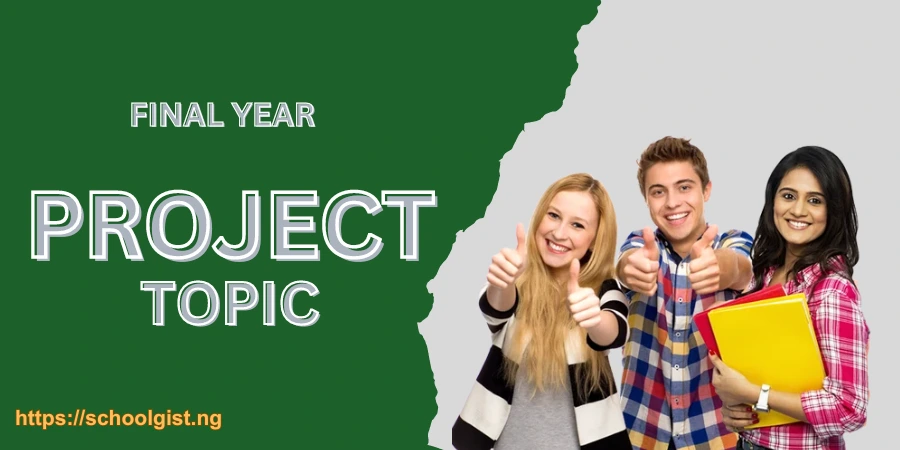
This project work titled EFFECT OF ACRYLIC POLYMER DISPERSIONS ON WATER VAPOUR PERMEABILITY AND SOME OTHER PHYSICAL PROPERTIES OF FINISHED LEATHERS has been deemed suitable for Final Year Students/Undergradutes in the Chemistry Department. However, if you believe that this project work will be helpful to you (irrespective of your department or discipline), then go ahead and get it (Scroll down to the end of this article for an instruction on how to get this project work).
Below is a brief overview of this Project Work.
Format: MS WORD
| Chapters: 1-5
| Pages: 81
EFFECT OF ACRYLIC POLYMER DISPERSIONS ON WATER VAPOUR PERMEABILITY AND SOME OTHER PHYSICAL PROPERTIES OF FINISHED LEATHERS
CHAPTER ONE
INTRODUCTION
1.1 BACKGROUND OF THE STUDY
Acrylics are esters of acrylic acids, which are the products formed by the reaction of an acrylic acid and alcohol. The esters of acrylic acid polymerise readily to form exceptionally clear plastics. These are widely used in applications requiring clear durable surfaces, e.g. in the aircraft and automobile industries. In more common use are surface coatings involving acrylics. The physical properties of acrylics (such as gloss, hardness, adhesion and flexibility) can be modified by altering the composition of the monomer mixture used in the polymerisation process. Acrylics are used in a wide range of industries, and the list below is simply a selection of some of the more common examples: Adhesives, textile industry (e.g. making sponge fill used in padded jackets), paper coatings, paint industry particularly in paints used for road markings.
The polymerisation process proceeds readily in the presence of catalysts and may be carried out in any one of four different ways: emulsion, bulk, solution or in suspension.
Emulsion polymerisation occurs in a water/monomer emulsion using a water-soluble catalyst. Emulsion polymerisation is the main process used in the production of acrylic polymers.
Bulk polymerisation is carried out in the absence of any solvent. The catalyst is mixed in with the monomer and the polymerisation is then left to occur with time. This is the method commonly used to manufacture acrylic sheets.
Solution polymerisation is carried out in a solvent in which both the monomer and subsequent polymer are soluble. Only low molecular weight polymers can be manufactured by this process, as high molecular weight polymers cause very high viscosities.
Suspension polymerisation is carried out in the presence of a solvent usually water, in which the monomer is insoluble, and in which it is suspended by agitation. To prevent the droplets of monomer from coalescing and also to prevent the polymer from coagulating, protective colloids are added. Suitable colloids include bentonite, starch, polyvinyl alcohol and magnesium silicate. In contrast to emulsion polymerisation the catalyst is monomer-soluble and is dissolved in the suspended droplets. The polymers are manufactured from monomers that are formed from the reactions of acrylic acids with alcohols. These are then polymerised using a radical initiator in a water emulsion.
The following components are needed for the emulsion polymerisation reaction: Monomer
Monomers are prepared by a reversible reaction between an acrylic acid and an alcohol:
CH2= CR-COOH + R’ OH CH2=CR-COOR’ + H2O Acrylic acid alcohol alkyl acrylate
The major monomers used are ethyl acrylate, methyl methacrylate and butyl acrylate, as well as non-acrylic monomers such as vinyl acetate and styrene which behave similarly.
Surfactant: A surfactant is a substance composed of mutually repellent polar and nonpolar ends. The surfactant surrounds each monomer droplet with a layer of surfactant with the polar tails oriented towards the surrounding water thus forming a micelle.
Water: Water is used as the medium to disperse these micelles. During the process the water acts as a solvent for the surfactants and initiators, as well as a heat transfer medium.
Initiator: The initiators (catalysts) usually used are water soluble peroxidic salts such as ammonium or sodium peroxydisulfate. The reaction can be initiated either by thermal or redox initiation.
In thermal initiation the peroxydisulfate dissociates to give two SO4–radicals.
–O3S—O—O—SO3– → 2SO4– • Peroxydisulfate sulfate radical
In redox initiation a reducing agent (usually Fe2+or Ag+) is used to provide one electron, causing the peroxydisulfate to dissociate into a sulfate radical and a sulfate ion:
Fe2+ + –O3S—O—O—SO3– → Fe3+ + SO4– • + SO42-
Peroxydisulfate sulfate radical
The emulsion polymerisation process can be carried out in a reaction kettle, which is fitted with a jacket for heating and cooling to allow control of temperature during the reaction.
Surfactant and water are first charged into the kettle. The monomer emulsion and initiator solution (containing redox agents to split the persulphate into sulphate radicals) is then transferred from the monomer feed tank into the kettle at a controlled rate. The mixture in the kettle is constantly agitated while the monomer is being added. During this time the monomer polymerises in accordance with the reactions given below:
.SO4 + CH2=CRCOOR‘ –OSO3 CH2 RC.COOR‘ Monomer monomer radical
. . SO CH C(COOR’) +CH=RC (COOR’) 4 2 2
Monomer radical
–SO CH -RC(COOR’)CH 2 RC. COOR’ 4 2
Dimer radical
Once the reaction has proceeded far enough to use up all the available polymerisation sites, the contents of the kettle are transferred to the stainless steel blend tank. The batch is then cooled, adjusted and transferred to holding tanks for storage and subsequent packing. The quality of the final product depends on the control exercised during the production process. Routine quality control checks of the following properties are carried out throughout the manufacturing process:
One of the most important tests of the finished polymer is determining its ‘glass transition temperature’, which is a measure of its toughness. This is done by heating the polymer at a constant rate and measuring its temperature. When a graph of time against polymer temperature is plotted, there will be points where the graph is flat, i.e. the polymer is being heated but it is not getting hotter. At these points the plastic is undergoing some sort of phase change between two different solid phases, and the heat energy is being used to rearrange the structure of the material rather than to simply heat it. Where these transitions occur and how many there are affects the toughness of the plastic.
Leather is made from hides and skins of animals. Large animals such as cattle have hides, small animals such as sheep have skins. The skin of any animal is largely composed of protein referred to as collagen, so it is the chemistry of this fibrous protein and the properties it confers to the skin with which the tanner is most concerned. Leather making is a traditional industry, which has been in existence since time immemorial, certainly over 5000 years, because the industry was established at the time of the Hammurabi Code (1795- 1750 BC) when Article 274 laid down the wages for tanners and curriers (Reed, 1972). Indeed, the use of animal skins is one of man‘s older technologies, perhaps only predated by tool making. In the modern world, the global leather industry exists because meat eating exists. Hence, most leather made around the world comes from cattle, sheep, pigs and goats. One of the byproducts of the meat industry is the hides and skins: considering that the annual kill of cattle alone is of the order of 300 million, such a byproduct, amounting to 10-20 million tonnes in weight, would pose a significant environmental impact if it were not used by tanners.
Skin is primarily composed of the protein collagen and it is the properties and potential for chemical modification of this protein that offer the tanner the opportunity to make a desirable product from an unappealing starting material, allowing it to be converted into a product that is both desirable and useful in modern life.
Collagen is a generic name for a family of at least 28 distinct collagen types, each serving different functions in animals, importantly as connective tissues (Bailey and Paul, 1998; Comper, 1996; Kichy et al., 1993; and Kadler, et al., 2007). The major component of skin is type I collagen. Unless otherwise specified, the term ‗collagen‘ will always refer to type I collagen.
Collagens are proteins, i.e. they are made up of amino acids. They can be separated into alpha amino acids and beta amino acids. Each one features a terminal amino group and a terminal carboxyl group, which become involved in the peptide link, and a side chain attached to the methylene group in the centre of the molecule.
In terms of the leather making, some amino acids are more important than others, since they play defined roles: the roles of importance are either in creating fibrous structure or involvement in the processing reactions for protein modification. Amino acids create macromolecules, proteins such as collagen by reacting via a condensation process.
An important part of the structure of collagen is the role of water, which is an integral part of the structure of collagen and hence their chemically modified derivatives (Bienkiewicz, 1990). Privalov, (1982) believed that the hydrogen bonding by water at hydroxyproline is important in stabilizing collagen but thought that the Ramachandran model (Ramachandran and Ramakrishnan, 1976) could not solely explain the high denaturation energy- rather the stabilization probably included wider layers of water. Privalov stated that having in mind the tendency of water molecules to cooperate with their neighbours; it does not seem improbable that the hydroxypropyl can serve as an initiator to an extensive network of hydrogen bonds. This envelops the collagen molecule and might be responsible for the exceptional thermodynamic properties of collagen.
Leather is used for various purposes including clothing, bookbinding, leather wallpaper, and as a furniture covering. It is produced in a wide variety of types and styles and is decorated by a wide range of techniques. Several tanning processes transform hides and skins into leather:
Vegetable-tanned leather is tanned using tannins and other ingredients found in different vegetable matter, such as tree bark prepared in bark mills, wood, leaves, fruits and rootsand other similar sources. It is supple and brown in color, with the exact shade depending on the mix of chemicals and the color of the skin. It is the only form of leather suitable for use in leather carving or stamping. Vegetable-tanned leather is not stable in water; it tends to discolor, so if left to soak and then dry it will shrink and become less supple, and harder. In hot water, it will shrink drastically and partly gelatinize, becoming rigid and eventually brittle. Boiled leather is an example of this, where the leather has been hardened by being immersed in hot water, or in boiled wax or similar substances. Historically, it was occasionally used as armor after hardening, and it has also been used for bookbinding.
Tanning by strict definition is the conversion of a putrescible organic material into a stable material that resists putrefaction by spoilage bacteria. Some of the features of tanning expected include the following:
The traditional way of thinking about tanning is based on the idea that the tanning agent confers stability to the collagen by changing the structure through crosslinking and thereby preventing the helices from unraveling: here is the first indication that a new concept of tanning is required, in which the function of the tanning agent is to prevent shrinking occurring by altering the thermodynamics of the process. The basis of the chrome tanning reaction is the matching of the reactivity of the chromium (III) salt with the reactivity of the collagen. The availability of ionized carboxyls varies over the range pH 2-6. This the reactivity ranges of collagen, since the metal salt only reacts with ionized carboxyls: the rate of reaction between chromium (III) and unionized carboxyls is so slow it can be neglected (Geher-Glucklich and Beck, 1971).
Chromium (III) salts are stable in the range pH 2-4, where the basicity changes, but at higher values they will precipitate. The development of modern chrome tanning went through three distinct phases:
Single bath process: the original process used chrome alum, Cr (SO4)3.K2SO4.24H2O, applied as the acidic salt, typically giving pH ≈ 2 in solution. Following penetration at that pH, when the collagen is unreactive, the system is basified to pH ≈ 4, with alkalis such as sodium hydroxide or sodium carbonate to fix the chrome to the collagen.
Two bath process: in this process which was an alternative approach to the single bath process, the technology of making chromium (III) tanning salts was conducted in situ to achieve a more astringent and efficient tannage. This means that the process is conducted in two steps. The pelt is saturated by chromic acid in the first bath, and then it is removed, usually to stand overnight. At this time, there is no reaction, because Cr (VI) salts do not complex with protein. The pelt is then immersed in a second bath, containing a solution of a reducing agent and enough alkali to ensure the final pH reaches at least 4. At the same time, processes were also devised that combined both valencies of chromium, exemplified by the Ochs‘ process (Ochs et al., 1953). However the dangers of using chromium (VI) drove change back to the single bath process. Not least of these considerations was the incidence of damage to workers by chromium (VI) compounds: the highly oxidizing nature of the reagents typically caused ulceration to the nasal septum.
Single bath process: with the development of masking to modify the reactivity of the chromium (III) salt and hence its reactivity in tanning, the global industry universally reverted to versions of the single bath process.
Chromium is a 3d44s2 element, so chromium (III) compounds have the electronic configuration 3d3, forming octahedral compounds. The hexaquo ion is acidic, ionizing as a weak acid or may be made basic by adding alkali. The hydroxyl species is unstable and dimerises, by creating bridging hydroxyl compounds because the oxygen of the hydroxyl confirm a dative bond via a lone pair. This process is called olation. It is a rapid, but not immediate reaction.
The work of Bjerrum, 1910, tells us how we can know that there `are hydroxyl bridges in these complex molecules.
Irving 1974 reviewed the chemistry of chromium (III) complexes from the point of view of the leather industry. Some of his more important observations can be summarized as follows:
Although the modern process is conventionally referred to as ‗chrome tanning‘, the reaction is most commonly conducted with basic chromium (III) sulfate, as the commonest reagent used in the global leather industry. The importance of that caveat lies in understanding the roles of every component of the salt and in reviewing the alternative options.
The reasons for the popularity of the process are clear, when the features of the process are compared with vegetable tanning:
CHAPTER ONE
INTRODUCTION
1.1 BACKGROUND OF THE STUDY
Acrylics are esters of acrylic acids, which are the products formed by the reaction of an acrylic acid and alcohol. The esters of acrylic acid polymerise readily to form exceptionally clear plastics. These are widely used in applications requiring clear durable surfaces, e.g. in the aircraft and automobile industries. In more common use are surface coatings involving acrylics. The physical properties of acrylics (such as gloss, hardness, adhesion and flexibility) can be modified by altering the composition of the monomer mixture used in the polymerisation process. Acrylics are used in a wide range of industries, and the list below is simply a selection of some of the more common examples: Adhesives, textile industry (e.g. making sponge fill used in padded jackets), paper coatings, paint industry particularly in paints used for road markings.
The polymerisation process proceeds readily in the presence of catalysts and may be carried out in any one of four different ways: emulsion, bulk, solution or in suspension.
Emulsion polymerisation occurs in a water/monomer emulsion using a water-soluble catalyst. Emulsion polymerisation is the main process used in the production of acrylic polymers.
Bulk polymerisation is carried out in the absence of any solvent. The catalyst is mixed in with the monomer and the polymerisation is then left to occur with time. This is the method commonly used to manufacture acrylic sheets.
Solution polymerisation is carried out in a solvent in which both the monomer and subsequent polymer are soluble. Only low molecular weight polymers can be manufactured by this process, as high molecular weight polymers cause very high viscosities.
Suspension polymerisation is carried out in the presence of a solvent usually water, in which the monomer is insoluble, and in which it is suspended by agitation. To prevent the droplets of monomer from coalescing and also to prevent the polymer from coagulating, protective colloids are added. Suitable colloids include bentonite, starch, polyvinyl alcohol and magnesium silicate. In contrast to emulsion polymerisation the catalyst is monomer-soluble and is dissolved in the suspended droplets. The polymers are manufactured from monomers that are formed from the reactions of acrylic acids with alcohols. These are then polymerised using a radical initiator in a water emulsion.
The following components are needed for the emulsion polymerisation reaction: Monomer
Monomers are prepared by a reversible reaction between an acrylic acid and an alcohol:
CH2= CR-COOH + R’ OH CH2=CR-COOR’ + H2O Acrylic acid alcohol alkyl acrylate
The major monomers used are ethyl acrylate, methyl methacrylate and butyl acrylate, as well as non-acrylic monomers such as vinyl acetate and styrene which behave similarly.
Surfactant: A surfactant is a substance composed of mutually repellent polar and nonpolar ends. The surfactant surrounds each monomer droplet with a layer of surfactant with the polar tails oriented towards the surrounding water thus forming a micelle.
Water: Water is used as the medium to disperse these micelles. During the process the water acts as a solvent for the surfactants and initiators, as well as a heat transfer medium.
Initiator: The initiators (catalysts) usually used are water soluble peroxidic salts such as ammonium or sodium peroxydisulfate. The reaction can be initiated either by thermal or redox initiation.
In thermal initiation the peroxydisulfate dissociates to give two SO4–radicals.
–O3S—O—O—SO3– → 2SO4– • Peroxydisulfate sulfate radical
In redox initiation a reducing agent (usually Fe2+or Ag+) is used to provide one electron, causing the peroxydisulfate to dissociate into a sulfate radical and a sulfate ion:
Fe2+ + –O3S—O—O—SO3– → Fe3+ + SO4– • + SO42-
Peroxydisulfate sulfate radical
The emulsion polymerisation process can be carried out in a reaction kettle, which is fitted with a jacket for heating and cooling to allow control of temperature during the reaction.
Surfactant and water are first charged into the kettle. The monomer emulsion and initiator solution (containing redox agents to split the persulphate into sulphate radicals) is then transferred from the monomer feed tank into the kettle at a controlled rate. The mixture in the kettle is constantly agitated while the monomer is being added. During this time the monomer polymerises in accordance with the reactions given below:
.SO4 + CH2=CRCOOR‘ –OSO3 CH2 RC.COOR‘ Monomer monomer radical
. . SO CH C(COOR’) +CH=RC (COOR’) 4 2 2
Monomer radical
–SO CH -RC(COOR’)CH 2 RC. COOR’ 4 2
Dimer radical
Once the reaction has proceeded far enough to use up all the available polymerisation sites, the contents of the kettle are transferred to the stainless steel blend tank. The batch is then cooled, adjusted and transferred to holding tanks for storage and subsequent packing. The quality of the final product depends on the control exercised during the production process. Routine quality control checks of the following properties are carried out throughout the manufacturing process:
One of the most important tests of the finished polymer is determining its ‘glass transition temperature’, which is a measure of its toughness. This is done by heating the polymer at a constant rate and measuring its temperature. When a graph of time against polymer temperature is plotted, there will be points where the graph is flat, i.e. the polymer is being heated but it is not getting hotter. At these points the plastic is undergoing some sort of phase change between two different solid phases, and the heat energy is being used to rearrange the structure of the material rather than to simply heat it. Where these transitions occur and how many there are affects the toughness of the plastic.
Leather is made from hides and skins of animals. Large animals such as cattle have hides, small animals such as sheep have skins. The skin of any animal is largely composed of protein referred to as collagen, so it is the chemistry of this fibrous protein and the properties it confers to the skin with which the tanner is most concerned. Leather making is a traditional industry, which has been in existence since time immemorial, certainly over 5000 years, because the industry was established at the time of the Hammurabi Code (1795- 1750 BC) when Article 274 laid down the wages for tanners and curriers (Reed, 1972). Indeed, the use of animal skins is one of man‘s older technologies, perhaps only predated by tool making. In the modern world, the global leather industry exists because meat eating exists. Hence, most leather made around the world comes from cattle, sheep, pigs and goats. One of the byproducts of the meat industry is the hides and skins: considering that the annual kill of cattle alone is of the order of 300 million, such a byproduct, amounting to 10-20 million tonnes in weight, would pose a significant environmental impact if it were not used by tanners.
Skin is primarily composed of the protein collagen and it is the properties and potential for chemical modification of this protein that offer the tanner the opportunity to make a desirable product from an unappealing starting material, allowing it to be converted into a product that is both desirable and useful in modern life.
Collagen is a generic name for a family of at least 28 distinct collagen types, each serving different functions in animals, importantly as connective tissues (Bailey and Paul, 1998; Comper, 1996; Kichy et al., 1993; and Kadler, et al., 2007). The major component of skin is type I collagen. Unless otherwise specified, the term ‗collagen‘ will always refer to type I collagen.
Collagens are proteins, i.e. they are made up of amino acids. They can be separated into alpha amino acids and beta amino acids. Each one features a terminal amino group and a terminal carboxyl group, which become involved in the peptide link, and a side chain attached to the methylene group in the centre of the molecule.
In terms of the leather making, some amino acids are more important than others, since they play defined roles: the roles of importance are either in creating fibrous structure or involvement in the processing reactions for protein modification. Amino acids create macromolecules, proteins such as collagen by reacting via a condensation process.
An important part of the structure of collagen is the role of water, which is an integral part of the structure of collagen and hence their chemically modified derivatives (Bienkiewicz, 1990). Privalov, (1982) believed that the hydrogen bonding by water at hydroxyproline is important in stabilizing collagen but thought that the Ramachandran model (Ramachandran and Ramakrishnan, 1976) could not solely explain the high denaturation energy- rather the stabilization probably included wider layers of water. Privalov stated that having in mind the tendency of water molecules to cooperate with their neighbours; it does not seem improbable that the hydroxypropyl can serve as an initiator to an extensive network of hydrogen bonds. This envelops the collagen molecule and might be responsible for the exceptional thermodynamic properties of collagen.
Leather is used for various purposes including clothing, bookbinding, leather wallpaper, and as a furniture covering. It is produced in a wide variety of types and styles and is decorated by a wide range of techniques. Several tanning processes transform hides and skins into leather:
Vegetable-tanned leather is tanned using tannins and other ingredients found in different vegetable matter, such as tree bark prepared in bark mills, wood, leaves, fruits and rootsand other similar sources. It is supple and brown in color, with the exact shade depending on the mix of chemicals and the color of the skin. It is the only form of leather suitable for use in leather carving or stamping. Vegetable-tanned leather is not stable in water; it tends to discolor, so if left to soak and then dry it will shrink and become less supple, and harder. In hot water, it will shrink drastically and partly gelatinize, becoming rigid and eventually brittle. Boiled leather is an example of this, where the leather has been hardened by being immersed in hot water, or in boiled wax or similar substances. Historically, it was occasionally used as armor after hardening, and it has also been used for bookbinding.
Tanning by strict definition is the conversion of a putrescible organic material into a stable material that resists putrefaction by spoilage bacteria. Some of the features of tanning expected include the following:
The traditional way of thinking about tanning is based on the idea that the tanning agent confers stability to the collagen by changing the structure through crosslinking and thereby preventing the helices from unraveling: here is the first indication that a new concept of tanning is required, in which the function of the tanning agent is to prevent shrinking occurring by altering the thermodynamics of the process. The basis of the chrome tanning reaction is the matching of the reactivity of the chromium (III) salt with the reactivity of the collagen. The availability of ionized carboxyls varies over the range pH 2-6. This the reactivity ranges of collagen, since the metal salt only reacts with ionized carboxyls: the rate of reaction between chromium (III) and unionized carboxyls is so slow it can be neglected (Geher-Glucklich and Beck, 1971).
Chromium (III) salts are stable in the range pH 2-4, where the basicity changes, but at higher values they will precipitate. The development of modern chrome tanning went through three distinct phases:
Single bath process: the original process used chrome alum, Cr (SO4)3.K2SO4.24H2O, applied as the acidic salt, typically giving pH ≈ 2 in solution. Following penetration at that pH, when the collagen is unreactive, the system is basified to pH ≈ 4, with alkalis such as sodium hydroxide or sodium carbonate to fix the chrome to the collagen.
Two bath process: in this process which was an alternative approach to the single bath process, the technology of making chromium (III) tanning salts was conducted in situ to achieve a more astringent and efficient tannage. This means that the process is conducted in two steps. The pelt is saturated by chromic acid in the first bath, and then it is removed, usually to stand overnight. At this time, there is no reaction, because Cr (VI) salts do not complex with protein. The pelt is then immersed in a second bath, containing a solution of a reducing agent and enough alkali to ensure the final pH reaches at least 4. At the same time, processes were also devised that combined both valencies of chromium, exemplified by the Ochs‘ process (Ochs et al., 1953). However the dangers of using chromium (VI) drove change back to the single bath process. Not least of these considerations was the incidence of damage to workers by chromium (VI) compounds: the highly oxidizing nature of the reagents typically caused ulceration to the nasal septum.
Single bath process: with the development of masking to modify the reactivity of the chromium (III) salt and hence its reactivity in tanning, the global industry universally reverted to versions of the single bath process.
Chromium is a 3d44s2 element, so chromium (III) compounds have the electronic configuration 3d3, forming octahedral compounds. The hexaquo ion is acidic, ionizing as a weak acid or may be made basic by adding alkali. The hydroxyl species is unstable and dimerises, by creating bridging hydroxyl compounds because the oxygen of the hydroxyl confirm a dative bond via a lone pair. This process is called olation. It is a rapid, but not immediate reaction.
The work of Bjerrum, 1910, tells us how we can know that there `are hydroxyl bridges in these complex molecules.
Irving 1974 reviewed the chemistry of chromium (III) complexes from the point of view of the leather industry. Some of his more important observations can be summarized as follows:
Although the modern process is conventionally referred to as ‗chrome tanning‘, the reaction is most commonly conducted with basic chromium (III) sulfate, as the commonest reagent used in the global leather industry. The importance of that caveat lies in understanding the roles of every component of the salt and in reviewing the alternative options.
The reasons for the popularity of the process are clear, when the features of the process are compared with vegetable tanning:
How to Download the Full Project Work for FREE
- You can download the Full Project Work for FREE by Clicking Here.
- On the other hand, you can make a payment of ₦6,000 and we will send the Full Project Work directly to your email address or to your Whatsapp. Clicking Here to Make Payment.