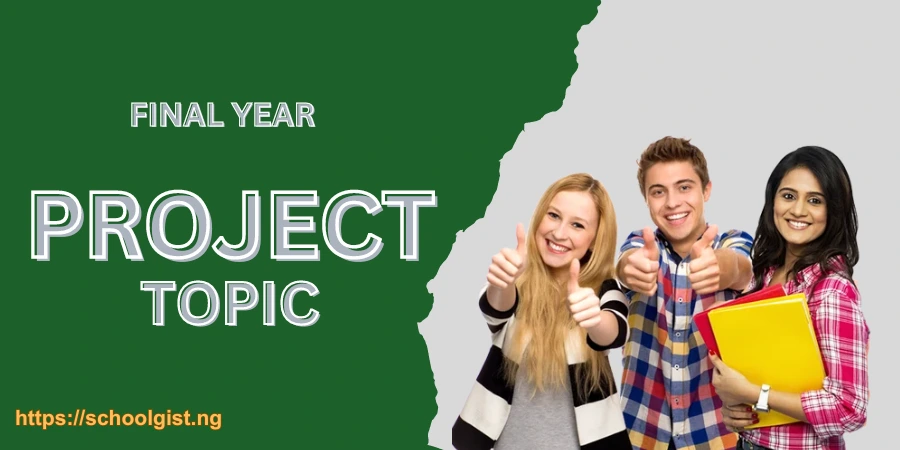
This project work titled DEVELOPMENT OF ENVIRONMENTALLY FRIENDLY BIODEGRADABLE CUTTING FLUID FROM SOYA BEANS (GLYCINE MAX) has been deemed suitable for Final Year Students/Undergradutes in the Mechanical Engineering Department. However, if you believe that this project work will be helpful to you (irrespective of your department or discipline), then go ahead and get it (Scroll down to the end of this article for an instruction on how to get this project work).
Below is a brief overview of this Project Work.
Format: MS WORD
| Chapters: 1-5
| Pages: 65
DEVELOPMENT OF ENVIRONMENTALLY FRIENDLY BIODEGRADABLE CUTTING FLUID FROM SOYA BEANS (GLYCINE MAX)
ABSTRACT
In this work, cutting fluid emulsion was developed from soya beans and the performance of the developed cutting fluid was evaluated by comparison with the conventional cutting fluid (control sample), using its ability to effectively perform as coolant during machining operation. The machining operation employed was the turning operation in which chips produced were collected and their surface finishes measured. The chips collected were evaluated for chip thickness ratio. Also, the temperature variations during cutting operation were measured using an infra- red gun thermometer. Temperature, surface finishing as well as chip formation rates using the developed cutting fluid under different cutting speed (rev/min), feed rate (mm/rev) and depth of cut (mm) was compared with that of the conventional cutting fluid. The average temperature of the work piece when developed cutting fluid was used as cutting fluid was 53.13 oC and that of the conventional cutting fluid was 54.7 oC. The result are very close, hence it shows better result in conducting heat away from cutting region. The developed cutting fluid gave an average high chip thickness of 0.446 mm while that of the conventional cutting fluid was found to be 0.316 mm. The high chip thickness of the developed cutting fluid is probably due to its better lubricating ability which allows easier and deep penetration of cutting tools. The average viscosity of the developed cutting fluid was found to be 31.1 poise at 29 oC, while the convectional cutting fluid was 47 poise at 29 oC. Low viscosity means high viscosity index, the developed cutting fluid has tendency to be fluid at higher temperature than the convectional fluid. In corrosion measurement, the developed cutting fluid shows no sign of corrosion; hence, the fluid has good ability to inhibit corrosion than the convectional cutting fluid.
CHAPTER ONE
INTRODUCTION
1.1 Background to the Study
The use of cutting fluids in metal cutting was first reported in 1894 by F. Taylor who noticed that cutting speed could be increased by 33% without reducing tool life by applying large amounts of water in the cutting zone (Ávila and Abrao, 2001). Cutting fluids increase tool life and improve the efficiency of the production systems providing both cooling and lubrication of the work surface. Cutting fluids are used to reduce the negative effects of heat and friction on both tool and work piece. Cutting fluids produce three positive effects on the process: heat removal, lubrication on the chip–tool interface and chip removal (Lopez de Lacalle et al., 2006).
ABSTRACT
In this work, cutting fluid emulsion was developed from soya beans and the performance of the developed cutting fluid was evaluated by comparison with the conventional cutting fluid (control sample), using its ability to effectively perform as coolant during machining operation. The machining operation employed was the turning operation in which chips produced were collected and their surface finishes measured. The chips collected were evaluated for chip thickness ratio. Also, the temperature variations during cutting operation were measured using an infra- red gun thermometer. Temperature, surface finishing as well as chip formation rates using the developed cutting fluid under different cutting speed (rev/min), feed rate (mm/rev) and depth of cut (mm) was compared with that of the conventional cutting fluid. The average temperature of the work piece when developed cutting fluid was used as cutting fluid was 53.13 oC and that of the conventional cutting fluid was 54.7 oC. The result are very close, hence it shows better result in conducting heat away from cutting region. The developed cutting fluid gave an average high chip thickness of 0.446 mm while that of the conventional cutting fluid was found to be 0.316 mm. The high chip thickness of the developed cutting fluid is probably due to its better lubricating ability which allows easier and deep penetration of cutting tools. The average viscosity of the developed cutting fluid was found to be 31.1 poise at 29 oC, while the convectional cutting fluid was 47 poise at 29 oC. Low viscosity means high viscosity index, the developed cutting fluid has tendency to be fluid at higher temperature than the convectional fluid. In corrosion measurement, the developed cutting fluid shows no sign of corrosion; hence, the fluid has good ability to inhibit corrosion than the convectional cutting fluid.
CHAPTER ONE
INTRODUCTION
1.1 Background to the Study
The use of cutting fluids in metal cutting was first reported in 1894 by F. Taylor who noticed that cutting speed could be increased by 33% without reducing tool life by applying large amounts of water in the cutting zone (Ávila and Abrao, 2001). Cutting fluids increase tool life and improve the efficiency of the production systems providing both cooling and lubrication of the work surface. Cutting fluids are used to reduce the negative effects of heat and friction on both tool and work piece. Cutting fluids produce three positive effects on the process: heat removal, lubrication on the chip–tool interface and chip removal (Lopez de Lacalle et al., 2006).
How to Download the Full Project Work for FREE
- You can download the Full Project Work for FREE by Clicking Here.
- On the other hand, you can make a payment of ₦5,000 and we will send the Full Project Work directly to your email address or to your Whatsapp. Clicking Here to Make Payment.