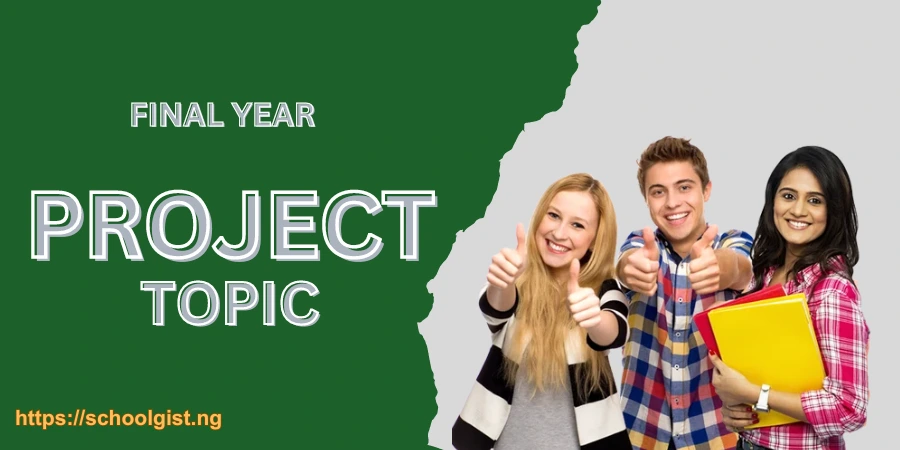
This project work titled DEVELOPMENT OF A COMPUTER PROGRAM FOR SOLIDS CONTROL has been deemed suitable for Final Year Students/Undergradutes in the Petroleum Engineering Department. However, if you believe that this project work will be helpful to you (irrespective of your department or discipline), then go ahead and get it (Scroll down to the end of this article for an instruction on how to get this project work).
Below is a brief overview of this Project Work.
Format: MS WORD
| Chapters: 1-5
| Pages: 74
DEVELOPMENT OF A COMPUTER PROGRAM FOR SOLIDS CONTROL
ABSTRACT
Computer software is used extensively to increase productivity and reduce man’s hours of labour. This work presents the development of a solids control software (SOLCON) which is designed for real time mud system management and quick performance of routine rig computations: determination of total solids and low gravity solids content; mud property and density control requiring optimal ejection rate into the mixing pit; volume of mud and amount of barite, bentonite and additives to be added during the upgrading process of the mud. This software has the ability to evaluate the need for dilution depending on the maximum allowable drilled solids, viscosity and recommended total solids in the drilling fluid. Finally, this software provides the atmosphere to control drilled solids as quickly as possible with all the necessary parameters.
CHAPTER ONE
FORMULATION OF THE PROBLEM
1.1 Introduction
Drilling fluid was introduced into the rotary drilling technology as means of transporting the drilled solids to the surface. Other function of the drilling fluids are controlling subsurface pressure, lubricating the drill string, cleaning the bottom of the hole, aiding in formation evaluation protecting formation productivity and aiding formation stability (Moore, 1986). One major function of the rig circulation system is the removal of drilled solids from the drilling mud before recirculation because of the adverse effects the drilled solids have on the drilling rate. One way of reducing drilling cost is the maximization of drilled solids removal from the drilling fluid (Field, 1972). For sometimes now the industry has battled with various unsatisfactory solutions to the problem of solids control. These included the following:
1. A piecemeal, temporary and very expensive way to reduce solids content is by discarding part of the system and rebuilding volume with added solids, water and chemical additives.
2. The use of „inhibitors‟ such as lime and polymers to reduce the contribution of drilled solids to mud. Generally, these materials only delays the time when a mud must be discarded.
3. A benefit more apparent than real way is the use „thinners‟. Thinners can reduce the gel strength and the yield point of the mud (Nelson, 1970).
There are direct and indirect costs associated with drilled solids. The direct cost involves dilution and discarding of the excess volume of mud. The indirect cost is connected to the increase mud weight resulting from the presence of drilled solids in the drilling fluid. This may results in pressure differential between the drilling fluid and the formation fluid and hence reduction in rate of penetration. A reduction in hole cleaning ability as result of an increase in plastic viscosity may also lead to reduction in rate of penetration and generation of finer cuttings (Wells, 1976). Low rate of penetration increases rig time and in tend increase the cost of drilling. In order to maintain a low specific gravity of solids in the drilling fluid, about one- quarter of the volume of the drilling fluid containing the drilled solids is removed.
The three basic way to control the concentration of drilled solids in drilling fluids are; removal of solids, adding solids or their equivalent and treating solids chemically. Soluble solids and clay is added to increase yield point, gel strength, plastic viscosity and decrease filtration rate with minimum weight increase. To increase the density of the mud, barite is added with minimum effect on the mud properties and solid volume. It is necessary to control the concentration of the drilled solids in the drilling fluid before returning it in to the drill pit. The more effectively the solids are mechanically removed the less dilution and hence the lesser the chemical treatment required (Moore, 1986).
ABSTRACT
Computer software is used extensively to increase productivity and reduce man’s hours of labour. This work presents the development of a solids control software (SOLCON) which is designed for real time mud system management and quick performance of routine rig computations: determination of total solids and low gravity solids content; mud property and density control requiring optimal ejection rate into the mixing pit; volume of mud and amount of barite, bentonite and additives to be added during the upgrading process of the mud. This software has the ability to evaluate the need for dilution depending on the maximum allowable drilled solids, viscosity and recommended total solids in the drilling fluid. Finally, this software provides the atmosphere to control drilled solids as quickly as possible with all the necessary parameters.
CHAPTER ONE
FORMULATION OF THE PROBLEM
1.1 Introduction
Drilling fluid was introduced into the rotary drilling technology as means of transporting the drilled solids to the surface. Other function of the drilling fluids are controlling subsurface pressure, lubricating the drill string, cleaning the bottom of the hole, aiding in formation evaluation protecting formation productivity and aiding formation stability (Moore, 1986). One major function of the rig circulation system is the removal of drilled solids from the drilling mud before recirculation because of the adverse effects the drilled solids have on the drilling rate. One way of reducing drilling cost is the maximization of drilled solids removal from the drilling fluid (Field, 1972). For sometimes now the industry has battled with various unsatisfactory solutions to the problem of solids control. These included the following:
1. A piecemeal, temporary and very expensive way to reduce solids content is by discarding part of the system and rebuilding volume with added solids, water and chemical additives.
2. The use of „inhibitors‟ such as lime and polymers to reduce the contribution of drilled solids to mud. Generally, these materials only delays the time when a mud must be discarded.
3. A benefit more apparent than real way is the use „thinners‟. Thinners can reduce the gel strength and the yield point of the mud (Nelson, 1970).
There are direct and indirect costs associated with drilled solids. The direct cost involves dilution and discarding of the excess volume of mud. The indirect cost is connected to the increase mud weight resulting from the presence of drilled solids in the drilling fluid. This may results in pressure differential between the drilling fluid and the formation fluid and hence reduction in rate of penetration. A reduction in hole cleaning ability as result of an increase in plastic viscosity may also lead to reduction in rate of penetration and generation of finer cuttings (Wells, 1976). Low rate of penetration increases rig time and in tend increase the cost of drilling. In order to maintain a low specific gravity of solids in the drilling fluid, about one- quarter of the volume of the drilling fluid containing the drilled solids is removed.
The three basic way to control the concentration of drilled solids in drilling fluids are; removal of solids, adding solids or their equivalent and treating solids chemically. Soluble solids and clay is added to increase yield point, gel strength, plastic viscosity and decrease filtration rate with minimum weight increase. To increase the density of the mud, barite is added with minimum effect on the mud properties and solid volume. It is necessary to control the concentration of the drilled solids in the drilling fluid before returning it in to the drill pit. The more effectively the solids are mechanically removed the less dilution and hence the lesser the chemical treatment required (Moore, 1986).
How to Download the Full Project Work for FREE
- You can download the Full Project Work for FREE by Clicking Here.
- On the other hand, you can make a payment of ₦5,000 and we will send the Full Project Work directly to your email address or to your Whatsapp. Clicking Here to Make Payment.