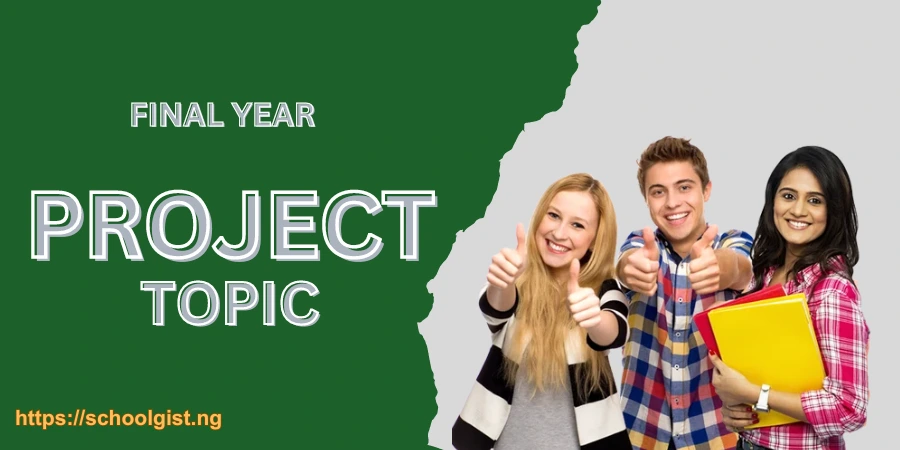
This project work titled DESIGN AND CONSTRUCTION OF CONTROL SYSTEM FOR DIRECT-ON-LINE STARTING OF INDUCTION MACHINE has been deemed suitable for Final Year Students/Undergradutes in the Electrical & Electronics Department. However, if you believe that this project work will be helpful to you (irrespective of your department or discipline), then go ahead and get it (Scroll down to the end of this article for an instruction on how to get this project work).
Below is a brief overview of this Project Work.
Format: MS WORD
| Chapters: 1-5
| Pages: 70
DESIGN AND CONSTRUCTION OF CONTROL SYSTEM FOR DIRECT-ON-LINE STARTING OF INDUCTION MACHINE
ABSTRACT
This project describes the methodical approach to the design and construction of control system for direct-on-line starting of induction machine. The procedures developed covers the construction of D.O.L stated for lower horse power motors. The prototype of this direct-on-Line starting of induction machine has been implemented following the methodical approach outlined in this project and its operational test and result are quite satisfactory. Adequate care has been taken in the design and construction of this project to ensure reliability. Therefore, the project is aimed at controlling the operation of single phase and three phase motors in industrial drive, companies, homes, laboratories and hospitals thereby reducing economic waste.
CHAPTER ONE
INTRODUCTION
BACKGROUND OF THE STUDY
Design and construction of control system for direct-on-line starting of induction machine: This is a control system that can control a single phase (1Ø) motors and three phase (3Ø) by making use of the components such as contactors, over current relay, start button, stop button etc. the contactors provides switching devices while over current relay is positioned to render protection to the machines in case of over current surge, the start and stop buttons called push buttons are used to start and stop the control contactor system. Again, there are pivot or indicator lamps which are controlled by normally open and normally closed of the auxiliary contacts incorporated to indicate when there is voltage supply to the three phase (3Ø) or single phase (1Ø) or both phases. However, the whole control system is controlled by mechanically pressing the push button ON and OFF when the circuit breaker has been switched ON.
The energy needed for the operation of the control system is three phase and one neutral through the input to produce single and three phase at the output terminal. Finally the mode of operation is shown on the circuit diagram of the control system. Organizational report:
In chapter, 1 discussed about the background, aim, scope and limitation of the project.
In chapter two, literature review of the project is discussed and elaborated.
In chapter three, Materials and methods is discussed.
In chapter four, Results and Discussion.
In chapter five, this is where the summary, conclusion and recommendation and references are stated.
Statement of Problem
The traditional methods of starting induction motors are direct-on-line starter, forward and reverse starter, star-delta starter, auto-transformer starter, and solid-state soft starter [1]. The conventional control methods of induction motors include: changing of the applied voltage, rotor resistance control, cascade control, pole changing schemes, stator voltage control, and vector control.
The main difference between a motor starter, and a motor controller is that, motor controllers do not provide overload protection, whilst motor starters provide protection for overload conditions of motors [2]. Control and starting methods are implemented on site or remotely using wires for connection. Wired control, attracts extra financial cost with respect to the required lengths of wires to cover the distance between the location of the motor and the control system, with the associated accessories to set it up. Motor control circuits are designed to perform a variety of functions; including: starting, stopping, reversing, and speed control [3. 4]. There are several different control methods, both wired, and wireless, that are used to control three-phase induction motors. Related works on motor controls are reviewed to appreciate the need to use infrared wireless transmission technology. The aim for the development of an infrared-based wireless transceiver to control a three-phase, 415 V, 50 Hz, squirrel-cage induction motor at remote and inaccessible areas was achieved in this research work.
OBJECTIVES OF THE STUDY
The aims/object of embarking on the project are:
1) To produce a system that will protect electric motor.
2) To design a control system that will start induction machines without causing damage to the equipment.
ABSTRACT
This project describes the methodical approach to the design and construction of control system for direct-on-line starting of induction machine. The procedures developed covers the construction of D.O.L stated for lower horse power motors. The prototype of this direct-on-Line starting of induction machine has been implemented following the methodical approach outlined in this project and its operational test and result are quite satisfactory. Adequate care has been taken in the design and construction of this project to ensure reliability. Therefore, the project is aimed at controlling the operation of single phase and three phase motors in industrial drive, companies, homes, laboratories and hospitals thereby reducing economic waste.
CHAPTER ONE
INTRODUCTION
BACKGROUND OF THE STUDY
Design and construction of control system for direct-on-line starting of induction machine: This is a control system that can control a single phase (1Ø) motors and three phase (3Ø) by making use of the components such as contactors, over current relay, start button, stop button etc. the contactors provides switching devices while over current relay is positioned to render protection to the machines in case of over current surge, the start and stop buttons called push buttons are used to start and stop the control contactor system. Again, there are pivot or indicator lamps which are controlled by normally open and normally closed of the auxiliary contacts incorporated to indicate when there is voltage supply to the three phase (3Ø) or single phase (1Ø) or both phases. However, the whole control system is controlled by mechanically pressing the push button ON and OFF when the circuit breaker has been switched ON.
The energy needed for the operation of the control system is three phase and one neutral through the input to produce single and three phase at the output terminal. Finally the mode of operation is shown on the circuit diagram of the control system. Organizational report:
In chapter, 1 discussed about the background, aim, scope and limitation of the project.
In chapter two, literature review of the project is discussed and elaborated.
In chapter three, Materials and methods is discussed.
In chapter four, Results and Discussion.
In chapter five, this is where the summary, conclusion and recommendation and references are stated.
Statement of Problem
The traditional methods of starting induction motors are direct-on-line starter, forward and reverse starter, star-delta starter, auto-transformer starter, and solid-state soft starter [1]. The conventional control methods of induction motors include: changing of the applied voltage, rotor resistance control, cascade control, pole changing schemes, stator voltage control, and vector control.
The main difference between a motor starter, and a motor controller is that, motor controllers do not provide overload protection, whilst motor starters provide protection for overload conditions of motors [2]. Control and starting methods are implemented on site or remotely using wires for connection. Wired control, attracts extra financial cost with respect to the required lengths of wires to cover the distance between the location of the motor and the control system, with the associated accessories to set it up. Motor control circuits are designed to perform a variety of functions; including: starting, stopping, reversing, and speed control [3. 4]. There are several different control methods, both wired, and wireless, that are used to control three-phase induction motors. Related works on motor controls are reviewed to appreciate the need to use infrared wireless transmission technology. The aim for the development of an infrared-based wireless transceiver to control a three-phase, 415 V, 50 Hz, squirrel-cage induction motor at remote and inaccessible areas was achieved in this research work.
OBJECTIVES OF THE STUDY
The aims/object of embarking on the project are:
1) To produce a system that will protect electric motor.
2) To design a control system that will start induction machines without causing damage to the equipment.
How to Download the Full Project Work for FREE
- You can download the Full Project Work for FREE by Clicking Here.
- On the other hand, you can make a payment of ₦5,000 and we will send the Full Project Work directly to your email address or to your Whatsapp. Clicking Here to Make Payment.